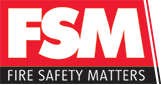
![]() |
Brian Sims
Editor |
Home> | Fire | >Manufacturing | >asecos focuses attentions on storage and handling of hazardous materials |
asecos focuses attentions on storage and handling of hazardous materials
20 July 2023
THE USE of safety storage cabinets and workstations for storing and handling hazardous substances has been established in many organisations. Such equipment is intended to provide the best possible levels of protection for a given organisation’s premises, its employees and the local environment. According to specialist cabinet developer asecos, the one-time purchase of technical equipment, though, is simply not enough.

During operation, regular maintenance by a competent individual ensures that the protective measures required by law function properly and provide the correct degree of protection.
For its part, the Government has issued strict regulations for the handling of hazardous substances in order to ensure the protection of people and the environment from toxic and aggressive chemicals. In the case of equipment designed to store hazardous substances in the workplace, the Government prescribes regular testing to ensure that the equipment functions correctly.
Requirements are set out in the Health and Safety at Work Act 1974, the Control of Substances Hazardous to Health Regulations 2002, the Provision and Use of Workplace Equipment Regulations 1998 and the Dangerous Substances and Explosive Atmospheres Regulations 2002.
If an organisation does not conduct maintenance measures for safety-related equipment, this could well have severe consequences. Potential prosecution is one. Under certain circumstances, insurance cover may not apply due to negligence, while a company’s liability limit might also also be waived.
Further, there can be significant incalculable costs, such as the impact on employee/visitor health, a production standstill and the potential need for the relocation of production or other logistical changes.
Put simply, any equipment intended for storing hazardous materials must be regularly inspected and all staff trained on how to use those products involved on the correct footing.
Who can inspect?
Multiple regulations require that all control measures relating to the storage and removal of hazardous materials must be inspected and maintained. For example, the aforementioned Control of Substances Hazardous to Health Regulations 2002 require that arrangements must be made for the maintenance of all hazardous substance storage facilities in the workplace. These arrangements, described as control measures, include extraction systems designed to contain and remove toxic, flammable or corrosive atmospheres.
Regulation 9 of the Control of Substances Hazardous to Health Regulations 2002 states that the employer must ensure those persons carrying out the inspections and testing for maintenance must be competent to do so and have the appropriate degree of knowledge and training and experience of methods and techniques relevant to the products used.
That individual is defined as someone who has the necessary expertise to test work equipment through their professional training and experience. For example, when it comes to storage cabinets, the inspection must be performed by the manufacturer or by persons authorised and trained by that manufacturer.
Risk assessment
For all asecos safety storage cabinets, the safety-related inspection process is mandatory. As previously mentioned, safety-related systems must be serviced and their functionality checked at regular intervals by a competent person. The basis for determining the inspection intervals is the risk assessment, which is mandatory for the employer.
The safety-related inspection provides huge comfort for end users – and, indeed, the host business as a whole – that all products intended to be used for the storing of hazardous material are functioning correctly.
As a manufacturer of safety cabinets designed to BS EN 14470 Part One and Part Two, asecos has now expanded its comprehensive service concept in the UK. The service team members thoroughly check all equipment and rectify any malfunctions on site, in doing so using original spare parts as well as any product upgrades that may be available.
A proven expert should always carry out the safety-related inspection of a safety storage cabinet. The best person for that job is a representative of the manufacturer of the cabinet.
Safety cabinets have several components: the fire protection construction (sealing systems), the technical extraction (air exchange, fire dampers and monitoring electronics) and special equipment such as the door arrest systems, pipe penetrations or similar.
In addition, the service technician will transact other work, such as filter replacement for recirculation filters.
*Further information is available online at www.asecos.com
- Safe storage of lithium-ion batteries addressed by asecos
- asecos focuses on safe storage of lithium-ion batteries
- asecos UK Academy introduces regular online seminar programme
- Safe storage of Lithium-ion batteries addressed by asecos at The Fire Safety Event
- asecos plans for “comprehensive three days” at The Fire Safety Event
- asecos teams up with Fire Safety Matters to run webinar on safe storage of compressed gas cylinders
- Making the grade
- Meet up with Asecos
- Handle with care
- asecos delivers trio of cabinets for safe lithium-ion battery storage