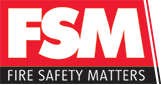
![]() |
Brian Sims
Editor |
Home> | Fire | >Manufacturing | >Making the grade |
Home> | Fire | >Risk Assessment | >Making the grade |
Making the grade
25 July 2018
Mark Whiteley explains why it is so important to understand the legislation but also meet the research and academic requirements.
STORING CHEMICALS in the research and academic environments can be a difficult balancing act between safety and practicality. Many laboratories require a vast range of chemicals to be stored close to the point of use and this presents many potential risks, not only from fire but also to health. Users of the chemicals, visitors to the laboratories and even the teams who are restocking the cabinets are all exposed in many different ways to the potential risks associated to those chemicals being stored.
European manufacturer of hazardous material storage cabinets, Asecos, strives to ensure that users have the right solution for the storage of chemicals at the point of use. To achieve this goal it is important that all clients are given the correct information and training respective to their unique requirements. Initially there are a number of objectives that must be observed.
Current legislation
There must be an understanding of the legislation governing storage by the end user, this may involve Asecos providing access to experts on hazardous material storage, providing training to safety managers, risk officers, laboratory managers and so on. EU legislation and guidance can be found within BS EN 14470, Segregation Guidelines (HSG) and safety data sheets amongst others. There is a need to understand Dangerous Substances and Explosive Atmospheres Regulations 2002, which is a legal requirement not only to have a risk assessment, but to have a DSEAR assessment. This is normally done by an external consultant, however it is possible to train a member of your team in DSEAR and its impact upon your workplace. Compliance with DSEAR is not optional, it is law and covers the use of chemicals, compressed gases and many other hazardous substances. Today many providers of safety equipment may lack the full knowledge of all specific legislation for the storage of chemicals, it is therefore essential you aim to research yourself what is required at your place of work.
At the point where you are familiar with the legislation and what is required in the way it affects your workplace, we can begin to look at how to store chemicals. The best way from our experience would be initially to identify all chemicals stored at your premises and then apply a method of segregation, The most comprehensive source of information for this is HSG71 providing detailed advice on the various classes of hazardous substances including compressed gases and how best to store those different classes safely in the same workplace.
The process of segregation can also benefit you in other ways; such as finding chemicals you never knew you had, or you simply have been buying too much, some organisations are being pushed by suppliers with special offers on chemicals where the procurement teams have no idea whether or not you will have sufficient storage to safely accommodate those chemicals. Why not decide to conduct a chemical amnesty, why pay for storage space on out date and overstocked chemicals. If the chemicals are out of date, over stocked or no longer used, then dispose of them safely, remove those skeletons from your cupboards
I would also like to explain further that many organisations now appear to be storing chemicals by families indicated by the GHS symbols, this can cause serious issues. Here is an example, the GHS symbol for flammables the black flame on a white background with a red diamond, covers four families of flammable chemicals, Flammable Liquids, Flammable Solids, Flammable Solids Spontaneously Combustible and Flammable Solids Hazardous When Wet. These four families share the same GHS symbol and at first glance you would assume they could be stored together, however, they cannot be stored together as you will see indicated in the document HSG71. This single point demonstrates the value of the guidance currently available.
Once all chemicals have been segregated according to in country guidelines, we can define the exact quantities and container sizes that are required to be stored. This leads to understanding which cabinets a user would need to procure. It is important at this stage to recognise that not all chemicals are required to be stored in fire resistant cabinets. New cabinets will need to be procured but where it is possible, the re-cycling of older metal cabinets can be used for non-flammable chemicals and corrosives, as long as they function correctly (such as the lock works and doors close) and the sumps present are sufficient to collect 110% of the total volume or 25% of the largest container whichever is greater. A large number of cabinets used for chemicals do not have any sumps as they may have been removed or re tasked elsewhere in the workplace, open the cabinets and check, it is that simple.
Flexibility and safety
When you require maximum flexibility in choosing the right location for your cabinet and the best way to mitigate the risk of spread of fire, then a fire-resistant cabinet manufactured to BS EN 14470 will offer you the best protection you can achieve worldwide today. You can store as much flammable liquid as the cabinet will hold in respect of volume and also they offer superb flexibility in respect of where the cabinets could be located. This is very important and quite useful when planning new laboratories or refurbishment.
One further point is shelf loading, BSEN14470 and BSEN14727 cabinet shelves are load tested. The load testing ensures that when you store the larger containers such as Winchesters you are safe in the knowledge the cabinet shelves will take the strain. Why invest in something which cannot protect your chemicals from fire, you from the chemicals and the best possible protection overall in daily use?
Next you would need to consider extraction, fume cabinets are designed to extract chemical fumes and gases from a process in that cabinet, exactly the same fumes can build up in an under bench storage cabinet, so there is no reason why one would be extracted and not the other. How many times have you opened up the flammables or corrosives cabinet and held your breath knowing the fumes and vapours are hazardous. A good storage cabinet connected to an extraction system on site will reduce the exposure of staff to potentially hazardous fumes and vapours. All of our cabinets come ready for connection to extraction, this quite simply assists in the removal of the harmful vapours of even the most general chemicals through LEV or recirculating extraction system. Quite simply why would you not extract the storage cabinets when you know the hazards presented by the safety data sheets? Do we all really need to be told to extract by legislation, or do we need to familiarise ourselves with the effect of mutagens, pathogens, teratogens and so on? Time to act is now! Flammables, corrosives and many more when inhaled can inflict potentially long-term damage on us as human beings. This is why glove manufacturers produce chemical resistant gloves, eyewear manufacturers produce chemical splash eyewear, and this is why cabinets used for storage need to be extracted.
Chemical manufacturers produce detailed data sheets in most cases for all chemicals, they are clear in explaining to a user what hazards are present for the chemicals they are handling and what precautions a user should take. Any person who comes into contact with a chemical in a workplace, has a duty to ensure that they are informed with regards to the hazards presented by that chemical. The hazards are not secret and are clearly described on the MSDS, which will offer guidance on how to interpret what PPE should be used and how to store the chemicals. You will find that as you grow through this process the MSDS may not give you enough advice and you will need to seek guidance elsewhere. Speak to your chemicals suppliers, speak to DSEAR professionals, you can also talk with storage specialists to build a picture of the safest possible way to store your chemicals
And finally, please do not also ignore your responsibilities under the Health and Safety at Work Act 1974 and your obligations to provide staff training on all aspects in the Use, Care and Maintenance of Safety equipment. This includes your storage cabinets. A reputable manufacturer or supplier will enable this training and awareness working with you on the best solution at your site. When was the last time you arranged for training on the use care and maintenance of your storage cabinets?
Mark Whiteley is UK sales manager at Asecos. For more information visit, www.asecos.com
- asecos focuses attentions on storage and handling of hazardous materials
- asecos unveils efficient air purifier for indoor areas
- Asecos building new training centre
- asecos plans for “comprehensive three days” at The Fire Safety Event
- Bryn Radford appointed in national service technician’s role at asecos
- asecos focuses on safe storage of lithium-ion batteries
- Battery back-up
- asecos UK Academy introduces regular online seminar programme
- asecos delivers trio of cabinets for safe lithium-ion battery storage
- ION-LINE PRO and ULTRA safety cabinets from asecos now VDMA-certified