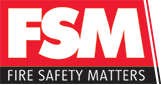
![]() |
Brian Sims
Editor |
Home> | Fire | >Business Continuity | >Handle with care |
Home> | Fire | >Risk Assessment | >Handle with care |
Handle with care
10 July 2021
The use of safety storage cabinets and workstations for the storage and handling of hazardous substances has become an established procedure in many of today’s organisations. Here, Mark Whiteley charts the regular maintenance regimes that are absolutely necessary to ensure sustainable safety
PROCURED STORAGE equipment for hazardous materials is intended to provide the best possible levels of protection for employees, the environment and, further, the host organisation’s premises. However, that one-time purchase of such technical equipment isn’t going to be enough. In fact, it’s merely the starting point. During operation, regular maintenance by a competent individual will ensure that the protective measures required by law also function properly and provide the correct safeguards.
The Government has issued strict regulations for the handling of hazardous substances to protect people and the environment from, for example, the potentially harmful impact of toxic and aggressive chemicals. In the case of equipment sourced to store hazardous substances in the workplace, the Government prescribes regular testing to ensure that it functions correctly.
Basic requirements in relation to testing regimes are set out in legislation including the Health and Safety at Work etc Act 1974, the Provision and Use of Workplace Equipment Regulations 1998, the Control of Substances Hazardous to Health Regulations 2002 and the Dangerous Substances and Explosive Atmospheres Regulations (the latter also issued back in 2002).
Health and Safety
In terms of the Health and Safety at Work etc Act 1974, it’s the duty of every employer to ensure, so far as is reasonably practicable, the health, safety and welfare at work of all employees. Without prejudice to the generality of an employer’s duty, the matters to which that duty extends include in particular the provision and maintenance of plant and systems of work that are, again so far as is reasonably practicable, safe and without risks to health.
The Dangerous Substances and Explosive Atmospheres Regulations 2002 refer to maintenance throughout. Having carried out all of the required assessment and subsequent implementation work, the employer should continue to ensure that the control measures subsequently created are maintained both in terms of hardware (ie plant, etc) and software.
The workplace, including the location of equipment, should be designed, constructed and maintained to prevent any release of dangerous substances accumulating in sufficient quantity that ignition could result in a fire and/or explosion or ‘other events’ that may lead to injury.
The Provision and Use of Work Equipment Regulations 1998 require that equipment provided for use at work is safe, maintained in a safe condition and inspected. To ensure that work equipment doesn’t deteriorate to the extent that it may put people at risk, employers and others in positions of control are required by the Provision and Use of Work Equipment Regulations 1998 to keep it maintained in an efficient condition and a good state of repair.
The frequency and nature of maintenance should be determined through risk assessment, taking full account of the manufacturer’s recommendations, intensity of use, the operating environment (encompassing the effects of temperature, corrosion and weathering), user knowledge and experience and also the potential risk posed to Health and Safety from any foreseeable failure or malfunction.
Put simply, if an organisation doesn’t conduct routine maintenance checks for its safety-related equipment, this will very likely have consequences. There’s the potential for prosecution. Under certain circumstances, insurance coverage may not be realised due to negligence, while the company’s liability limit could also be waived. On top of all that, there can be enormous and sometimes incalculable costs due to production line standstill, the necessary relocation of production facilities or the forced introduction of logistical alterations.
Inspection regime
Multiple regulations require that all control measures relating to the storage and removal of hazardous materials must be inspected and maintained. For example, the aforementioned Control of Substances Hazardous to Health Regulations 2002 require that arrangements must be made for the maintenance of all hazardous substance storage facilities in the workplace. These arrangements, which are commonly described as control measures, include those extraction systems designed to contain and/or remove toxic, flammable or corrosive elements from the atmosphere.
Regulation 9 of the Control of Substances Hazardous to Health Regulations 2002 states that the employer must ensure those individuals carrying out the inspections and testing for maintenance are competent to do so and have the appropriate levels of knowledge, training and experience of the methods and techniques relevant to the products being used. These individuals are defined as people who harbour the necessary expertise to test work equipment through their professional training and experience. When it comes to safety storage cabinets, the inspection must be performed by the manufacturer or by persons authorised and trained to do so by that manufacturer.
For all asecos-produced safety storage cabinets, safety-related inspections are mandatory. As already mentioned, safety-related systems must be serviced and their functionality checked at regular intervals by a competent person. The basis for determining the inspection intervals is the risk assessment, which is mandatory for the employer. The safety-related inspection provides peace of mind for end users and the business that all products intended for the storage of hazardous material are functioning correctly.
In practice, the service technician will thoroughly check all storage equipment and rectify any malfunctions on site, using original spare parts as well as any product upgrades that may be available in order to do so. Again, it should be a proven expert who conducts the safety-related inspection of a safety storage cabinet and the best person for that role is someone representing the manufacturer of the cabinet.
Considerations involved will include the fire protection construction (ie sealing systems), the technical extraction (ie air exchange, fire dampers and the monitoring electronics) and also special equipment such as the door arrest systems, pipe penetrations or similar. Typically, the service technician will also carry out other work including filter replacements for recirculation filters.
Procedure in detail
What, exactly, is the safety inspection process for a given safety storage cabinet? By way of example, the main features of a safety inspection for a Type 90 safety cabinet for the storage of flammable liquids will usually include a functional test, a safety check, a fire protection test, a ventilation test, a legal safety check, visual inspection and, if deemed necessary, the repair and replacement of specific parts.
During the inspection of safety storage cabinets for flammable liquids, a visual inspection is carried out to check for general damage to the entire cabinet and look for any corrosion of drip pans, for instance. The service technician checks by re-measurement that the alignment of the cabinet and the gap dimensions of the doors comply with the regulations.
On that note, the functional check includes testing for proper door closure. What sounds trivial is particularly important for protection performance as doors that are not fully closed would promote heat penetration in the event of a fire. At the end of the day, such a scenario is precisely what the storage cabinet is supposed to prevent. During the functional test, all safety aspects and fire protection functions are examined, including whether or not the seals required for fire protection are present and intact.
If the cabinet is technically ventilated, a ventilation test is then also performed: Exhaust air measurements are used to determine whether the cabinet achieves the prescribed exhaust air volume. In the case of safety cabinets operated without technical ventilation, the service technician assesses compliance with the explosion protection zones and current regulations on request.
During the optional legal safety check, checks to determine the correct labelling is present or whether the collection volume of the prescribed floor collection tray is sufficient for the storage volume are conducted. The technician will make sure that all safety-related equipment is in working order and put right any malfunctions directly during the inspection process. If spare parts are needed because a minor repair‘s required, the technician will usually have the necessary parts to hand for installation.
Finally, the technician documents the work carried out and completes a test report such that the company is covered in the event of damage. This protocol, as well as a test sticker for the cabinet, documents a professionally performed inspection. All work carried out and the inspection itself will be covered by a one-year warranty. Following this initial certification, all customers are automatically notified of when the next safety inspection is due, which subsequently enables them to maintain their insurance cover.
Ensuring product reliability
One of our own service technicians, namely Bryn Radford, has extensive experience in the health, safety and engineering sectors. His background includes ten years as a CBRN instructor for the Ministry of Defence, during which time he completed many training courses (among them the IOSH Managing Safety course). He has a wealth of experience in M&E engineering. Ultimately, this means that he can conduct all essential maintenance and repairs on the range of safety cabinets that we produce.
On joining the business, Bryn undertook a comprehensive in-house training programme and receives regular practical instruction on the relevant products to ensure that he‘s always able to offer high quality and competent service routines. In addition, Bryn provides on-site customer training such that client organisations have the necessary technical support available when it‘s needed.
“Planned maintenance and regular inspection is key to ensuring product reliability,” observed Bryn. “Our cabinets are made to a specific standard. To ensure that standard is upheld, annual inspections must be carried out. I’m always working closely with our team in Germany to plan and schedule safety inspections, maintenance and repair visits for customers nationwide.”
Our clients include a variety of universities and laboratories as well as industrial businesses. As such, there’s no typical daily routine when it comes to servicing and maintenance. Behind every order there’s a customer with individual queries and challenging questions that demand to be addressed and answered as quickly as possible. Doing so is very much a core mission for the business.
Mark Whiteley is UK and Ireland Manager for asecos (www.asecos.com)
- asecos focuses on safe storage of lithium-ion batteries
- asecos teams up with Fire Safety Matters to run webinar on safe storage of compressed gas cylinders
- Live chemical explosion demonstrations
- asecos focuses attentions on storage and handling of hazardous materials
- ION-LINE PRO and ULTRA safety cabinets from asecos now VDMA-certified
- Battery back-up
- Advice on safe storage of compressed gas cylinders delivered by asecos
- Chemical reaction
- asecos unveils efficient air purifier for indoor areas
- Tested, GS-certified and safe: the ION-LINE ULTRA from asecos