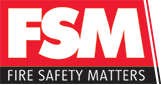
![]() |
Brian Sims
Editor |
Home> | Fire | >Risk Assessment | >Burning rubber |
Burning rubber
10 July 2021
Rubber and plastic recycling often relies on high volume storage for long periods of time alongside intense processing to repurpose these materials for fuel, construction or other uses. James Mountain explores the associated fire risks, including business owners’ responsibilities and measures that can be taken to mitigate those risks

THE GLOBAL drive towards sustainability is witnessing a rise in rubber and plastic recycling across the UK at a rate that’s only expected to continue to grow. This brings into play significant fire risks, as evidenced by the somewhat troubling fire record for recycling plants.
The plastics industry has been one of the fastest developing sectors since World War II, with the forms and adaptations of plastics creating an unusually complicated and diverse family of materials. The rubber industry is also seeing a combination of raw materials in play, with today’s tyres comprising over 200 different raw materials and the average car tyre comprising approximately 30 types of synthetic rubber and eight types of natural rubber. Many of the ingredients used in the modern day manufacture of rubber and plastics are combustible, in turn lifting the materials’ fire risk.
Both plastic and rubber fires are more oil-based than other material fires, meaning that they can often act more like a flammable liquid fire when ignited. This renders fire suppression more challenging.
As a material, rubber doesn’t readily ignite, but when it is alight, the spread of fire and smoke can be rapid, with the material burning at extremely high temperatures. At 200°C, rubber begins to flow as a hot mass. At 230°C, it emits flammable vapours that can become trapped in the molten rubber. This can catch fire with an explosive force if not controlled quickly enough.
As rubber naturally repels water, many extinguishing mediums are often shed and drained away. Often, traditional suppression measures, such as sprinklers at the ceiling level, will be limited in their ability to control rubber-based fires.
Tyre fires
Tyre fires are considered to be the most common type of rubber fires as waste tyres are often stacked and stored for long periods of time before being repurposed for use as a sustainable fuel or to produce rubber crumb or tyre shred. Before being recycled, rubber tyres are often stored in large stockpiles which present key fire risks due to the air spaces present between tyres and their potential for high heat output. Additionally, due to their shape, if a fire were to burn inside a tyre, it’s even harder to extinguish as it’s challenging to penetrate the inside of the tyre with any extinguishing agent.
Burning tyres release a range of toxic chemicals, including carbon monoxide and nitrogen oxides. They also release substantial quantities of oil, with one million tyres releasing up to 208,198 litres. In this instance, foam extinguishers are often more suitable than water-based systems.
Tyre fires can also burn for a long time. The tyre dump fire at Heyop in Wales back in October 1989 took an astonishing 15 years to fully extinguish as the tyres were so densely packed together, allowing the blaze to smoulder beneath the surface until 2004.
Once ready to be recycled, tyres are often shredded into smaller chips. This process produces a low-density material which allows air to pass through and covers a high surface area. Each of these characteristics make the shredded material susceptible to self-combustion. This commonly occurs in large stockpiles where ventilation is low. Laboratory experiments show tyre shred and rubber crumb to be more susceptible to self-combustion than cellulosic materials – such as hay or straw – in high ambient temperatures.
All that said, fires within piles of tyre shred or rubber crumb often take weeks to initiate, making prevention perfectly possible in many scenarios.
The plastic risk
Both the naturally occurring and man-made polymers that make up plastics behave similarly when exposed to fire, often producing highly toxic chemicals when ignited. The rate of burn and smoke emitted varies widely depending on the specific type of plastic and-flame retardant chemicals present in the material. Flames from plastics generally spread quickly. Cellulose nitrate plastic is one of the most flammable types of plastic and, much like tyres and rubber, is capable of self-ignition when exposed to heat.
Burning plastic can produce large volumes of thick, black smoke. Any chemical additives in the plastic can accelerate this smoke production still further. Like rubber at high temperatures, plastics will melt and run, causing fires to spread in different – and, sometimes, unpredictable – ways.
When recycled, plastics are commonly used for the production of renewable fuels such as solid recovered fuel (SRF) and refuse-derived fuel (RDF). This process brings about a number of key fire risks. The resulting materials are highly flammable, requiring careful planning and consideration for risk mitigation.
Subcoal technology is now being used to upgrade SRF and RDF into pellets, which can then be used as alternatives to coal or lignite to fuel industrial furnaces, such as lime or cement kilns or coal-fired power stations. This material often has a calorific value that-s comparable with – and sometimes higher than – certain coals, which makes it highly susceptible to fire risk when stored in stockpiles.
Responsibilities and regulations
As the Environment Agency continues to strengthen its enforcement of regulations pertaining to fire safety at waste and recycling sites, ensuring that the host business has a robust fire prevention plan in place is essential. That plan needs to outline all fire prevention measures and policies, including the risks pertaining to the business and the mitigation measures in place to control those risks.
The Regulatory Reform (Fire Safety) Order 2005 signposts business owners’ responsibility to ensure that reasonable steps are taken to mitigate fire risk on site. Where the risk is greater, such as for those businesses dealing with rubber and plastics, measures should be considered carefully and regularly reviewed to circumvent any weaknesses.
General workplace Health and Safety guidance is outlined in both the Health and Safety at Work etc Act 1974 and the Management of Health and Safety at Work Regulations 1999. There’s also specific voluntary guidance surrounding the storage of rubber (ISO 2230:2002) and the suitable use of certain fire prevention and suppression systems and how to handle particular kinds of fires (reference NFPA 11 and EN 13565).
Safeguarding rubber and plastics
Ensuring safety for sites handling rubber and plastics requires focus on three key areas: initial bulk storage of the raw materials, the process for recycling or repurposing the materials and the bulk storage of the newly-formed materials. Each of these processes may not be relevant for every site, but they offer an overview of the different aspects to be considered and accounted for when looking to reduce the risk of rubber and plastics fires.
There are various steps that can be taken to minimise the risks associated with bulk storage of raw materials. From a materials point of view, they include regular sub-surface temperature monitoring, control of moisture levels and adequate ventilation. In terms of the storage piles, it’s best to consider minimising the size of the piles, ensuring separation (either physically or using fire walls) between all waste piles and managing the stock to ensure materials are not stored for long periods of time.
When it comes to selecting a fire prevention or suppression system to monitor these factors and mitigate fire risk further, the consideration and focus should be on using a compressed air foam system as this will allow the agent to stick to the materials, excluding any oxygen and suppressing the fire.
When processing rubber and plastics for re-use as an alternative fuel source in the form of SRF or RDF, fire risk is extremely high and mitigation measures will often require an holistic approach. That approach starts with planned preventative maintenance. Rubber and plastic will emit small particles when shredded. If not monitored and cleaned regularly, these can build up in particular areas within the machinery, such as on bearings or in drive enclosures, and become prone to self-combustion, propelled by the heat emitted from the machinery when in use, and particularly so if the machinery is in use for long periods. Regular maintenance will help to minimise risk of mechanical failure or friction which can lead to an increased fire risk.
In terms of fire prevention systems, specific parts of the processing machine (eg shredders) will often require localised application protection. Detection systems (eg linear heat detection, infrared flame detection or video flame detection) are also important to monitor for flames, sparks or embers which can form from metallic presence within the materials, for example.
Storing processed materials
As is the case with the storage of the raw materials, regular controls and checks can help to minimise fire risk in processed materials. The checking regime may include turning piles at regular intervals where the risk of self-combustion or spontaneous heating is higher, regularly monitoring sub-surface temperatures and controlling both moisture levels and material risk factors (eg any exposed metal content).
Processed rubber and plastic in the form of SRF or RDF, for example, has a high calorific value. A fire may be deep seated among the fibrous materials, meaning that a Class A penetrating foam system using deluge systems, cannons/monitors or hose reels systems will likely be most effective. This focuses a high flow of water with a foam additive on a particular area, enabling it to reach beneath the material surface and suppress the fire at the point of ignition.
Supporting any fire mitigation measures with a full fire risk assessment is critical. This will render the solution tailored to the individual site and its risks, while accounting for considerations such as the amount of material being stored, the form in which it’s stored and the processing activity such that prevention measures and systems are best placed to mitigate present risks.
James Mountain is Sales and Marketing Director at Fire Shield Systems (www.fireshieldsystemsltd.co.uk)
- Fire on railway track
- Fire and Security Matters Awards 2023 open for entries
- Care home admits fire safety breaches
- King’s Cross firefighter honoured by FBU at Red Plaque unveiling
- Leaseholders protected as building safety reforms come into force
- Bicycle Association launches ‘Stop e-Bike Fires’ Action Plan for Government
- Election campaign turns focus to security
- Conman jailed for software fraud
- Technical Bulletin released to support compliant Fire Alarm Zone Plans
- Ministry of Housing, Communities and Local Government announces £30 million ‘Waking Watch’ Relief Fund