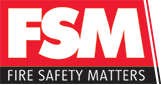
![]() |
Brian Sims
Editor |
Home> | Fire | >Evacuation | >Quarts and Pint Pots |
Home> | Fire | >Risk Assessment | >Quarts and Pint Pots |
Quarts and Pint Pots
02 October 2020
Fire safety requirements for rail networks operating within airports pose a unique set of challenges for design teams and, indeed, demand specific management protocols given what can be large occupancy numbers combined with 24-hour services. Here, Tony Cash reviews the key factors considered for the Terminal Transit System at Heathrow Airport’s Terminal 5
HEATHROW AIRPORT’s Terminal 5 was designed in the late 1990s and into the early 2000s. Physical construction began in 2002 and the Richard Rogers Partnership-fashioned building (the main element of which is the largest free-standing structure in the UK) was officially opened six years later on 14 March. Engineers on the project were from Arup and Mott MacDonald.
The celebrated building cost £4 billion and took almost 20 years from conception to completion, necessitating what became the longest public inquiry in British history. The building was designed to handle a throughput of 35 million passengers every year. In 2018, Terminal 5 handled 32.1 million passengers on 211,000 flights. It was the busiest terminal at the airport, measured both by passenger numbers and flight movements.
On opening to the public, an ‘as-built’ description of the fire precautions was produced for the airport’s operator (back then the British Airports Authority). For its part, the Terminal Transit System (TTS) was designed to connect Terminal 5A to Terminal 5B and, eventually, would join Terminal 5C. Running tunnels and three stations (one each for Terminal 5A, 5B and 5C) would feature platform edge screens and doors, safe walking routes along the entire length of the track and a maintenance facility at the end of Terminal 5C.
Unlike a traditional underground system, the TTS is not a ‘Metro’ and nor is it anything like ‘Heavy Rail’. Rather, it’s a track-guided system using a centre rail to help steer the rail vehicles on their route and provide power.
Fire protection
The principles of fire protection were enshrined within, first of all, the Airport Fire Safety Plan from which the Master Fire Safety Plan for the Terminals (in this case the whole campus of Terminal 5) was derived. This then gave rise to the overarching TTS Fire Safety Plan. Any significant change to any of the features of the airport terminal, or of the TTS, should trigger an impact assessment of them to preserve compliance with the Airport Fire Safety Plan.
It’s worth noting that the Regulatory Reform (Fire Safety) Order (RRO) had not been fully enacted at the time of design and the ‘1989’ Sub-Surface Railway Stations Regulations were still in force under the Fire Precautions Act 1971. These were heavily impacted by the drafting of the RRO and among the reasons why the latter suffered a somewhat rough journey in Parliament.
The TTS wasn’t a railway in the true sense of the word. There were no train operators, for example, and unlike the Docklands Light Railway, no train captain and no station staff, either. It was the unattended or the unstaffed nature of this underground light rail system which made it complicated.
There were dominant factors for consideration at the time. The reduction (and method) of keeping the risk of ignition low and reducing or eliminating fire development. Important clauses on the material selection (internal and external). Fire separating elements (for example, a fire barrier test specified with a duration of 20 minutes). An assessment of how rail vehicles would continue to operate in the event of fire (ie running capability). The need for a concise and precise operating and maintenance manual. Specific measures to be included for emergency lighting, safety equipment and the information provided to passengers on evacuation requirements.
Common Safety Method
With the passage of time, there is, today, an opportunity to reference the Common Safety Method and realise that adherence to British Standards themselves does not protect the infrastructure in which the TTS operates. This was the basis of the challenge faced when the airport’s operator decided to replace the existing rolling stock with new which would also include the advent of longer trains.
PAS 911 has not enjoyed a tremendous following or uptake, whereas BS 9997: Fire Safety Management has had a smoother ride. It’s for this very reason that a British Standard on fire safety measures and operations at airports would be very welcome, just like the recently launched BS 9992 has been within the rail community. It’s a pre-requisite that qualified and experienced fire safety professionals produce the fire strategy and define, for instance, the level of fire detection and alarms and also produce a ‘Cause and Effect’ Schedule.
Competency can be evidenced in many ways as exemplified by the recent contributors to British Standard 9992. It has been shown by the Grenfell Tower Inquiry just how important it is to keep a record of qualifications, experience and Continuing Professional Development. A number of automated record-keeping processes exist for this purpose. It’s worth noting here that the UK’s Civil Aviation Authority has found the Redkite system to have a demonstrable track record in this regard.
In the case of a fire strategy, it’s simply not adequate to divide up life safety requirements and farm them out to the electrical engineer, the mechanical engineer, a human factors specialist or a building management consultant. It needs a persistent supervisory approach from a sector-competent fire engineer to assess the impact that the sum of all parts of an environment affording life safety in case of fire will have on the whole fire safety lifecycle.
It’s also important to recognise that there’s more than one approving entity. Each and every one of them needs to be consulted and notified. In the case of the TTS, this means the London Fire Brigade and the Office of Rail and Road, the Department for Transport (which sets the security requirements that airports must respect), the Landlord and the tenants (for example, the airlines have an interest) and the adjoining transport providers (eg rail companies for heavy rail and, perhaps, London Underground for Metro all have a stakeholder interest in the piece).
Compartmentation issue
A particular challenge has been that fire safety by construction did not include compartmentation between the platforms and the terminal buildings as a whole and, therefore, could not be relied upon. Horizontal separation between stations along the trackway is also not present, allowing smoke and the toxicity products of combustion to move freely along the routeway by air movement.
An effective solution relying on the ventilation of smoke and toxic fumes has been important to increase time for evacuation and also to assist the Emergency Services because there are limited routes for access by the Fire and Rescue Service. Response is also not instantaneous. It’s important to recognise that, in the UK, the Airport Fire and Rescue Service is not there for so-called ‘domestic’ calls. Rather, its main purpose is to protect the aircraft.
The local authority fire services need to be escorted to the seat of the fire by the Airport Fire and Rescue Service or airport operations. This all adds time to the response objective. It’s therefore really important to limit fire spread and growth by using materials that have been wisely chosen and specified.
At the time of design, the type of rail vehicle chosen for the transit was a new one using materials that were innovative and not fully elaborated. In today’s design and build, extensive testing does have to be caried out and a Fire Certificate Inventory List produced for all the significant parts of a rail vehicle.
The rail vehicle comprised a composite body shell, seats, the vehicle interior and linings, rubber tyres, rubber seals, cabling and, of course, in the airport environment, passengers would be bringing luggage on board.
Another important factor was the fatal accident in Kaprun on 11 November 2000. As the operating company’s technical experts kept pointing out, the train was “fire-proof”. Made of tough aluminium, it was able to transport 180 people in one go in an upwards direction, while the downward carriages would be carrying up to 180 people simultaneously. Tragically, 155 people died in the fire (150 on the ascending train, two on the descending train and three in the mountain station).
Safety case approach
The TTS Basis of Design took a safety case approach – one that’s familiar at airports, in fact – with an assessment made of the systems and each of its sub-systems to ensure the target level of safety was at least as good as the current system and, certainly, no worse at any point in the future.
The maximum heat release rate was contractually required to be no more than that of the existing vehicles in their ‘as-built’ condition, even though the selection of the fire properties of the materials had not been fully understood at the time of original design. This was a huge hurdle to overcome and considerable negotiations took place across many hours of discussion. The outcome was a contractual document with fire safety requirements firmly written into a contract harbouring nearly 700 clauses.
Specific heat release rates had been determined for a fire in the tunnel, a fire under the train in a station and for a fire inside the train at the station (with the assumption that the windows would remain intact). The inclusion of water mist suppression in the maintenance area allowed the heat release rate to be reduced to an equivalent of a sprinkler-controlled fire.
The UK Railway Safety Principals Guide 2b for stations and the USA NFPA 130 Codes of Practice informed the fire strategy, the objectives of which were to limit financial loss, the loss of connections between terminals, missed flights, lost revenue, unwanted air navigation charges for delayed aircraft, unwanted ground handling fees for delayed pushback and (more recently in Europe) the requirement for an airline to pay enhanced compensation for denied boarding of flights.
For any circumstances within the airport’s control, it was well worth the investment of time to ‘get it right’ when procuring the new rail cars. BS 6853 was chosen in preference to the emerging EN 45545 as the British Standard was considered more mature and robust whereas it was felt that the European Norm allowed far too much of a relaxation of fire, smoke and toxic species properties.
Ultimately, at the conclusion of this work there will be a more efficient and more frequent transit service, more happy passengers and less missed flights when air transport begins to pick up once again in the wake of COVID-19.
Dr Tony Cash BSc PhD CChem FRSC EurChem CEng FIFire is an Independent Chartered Fire Engineer and President of the Rail Industry Fire Association (www.rifa-rail.co.uk)
- Restaurant duo sentenced over inadequate fire safety measures
- Calls for security and fire safety personnel to be designated as “key workers”
- NFCC launches maturity models and Workforce Good Practice Framework
- Mayor presents award to fire commissioner
- COVID-19 and the Business World: A Risky Return to Reality
- ExcelRedstone to deploy Maxxess eFusion integration at City of London development
- Security industry campaign “to reset perceptions of security officers in public domain”
- New head of Insurance Fraud Enforcement Department
- Grenfell Tower Public Inquiry: “Politicians must take brunt of blame” asserts LFB
- Construction Products Association to chair Industry Competence Steering Group