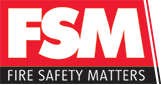
![]() |
Brian Sims
Editor |
Home> | Fire | >Risk Assessment | >No time to waste |
Home> | Fire | >Suppression | >No time to waste |
No time to waste
01 March 2021
In recent years, the waste and recycling and waste-to-energy sectors have taken significant strides to improve fire safety, with the Environment Agency making Fire Prevention Plans mandatory for all businesses operating within the industry. However, as James Mountain explains there’s further ground yet to be covered and insurers, it seems, have a key role to play.

THE WASTE and recycling and waste-to-energy sectors are prone to multiple fire risks. The ongoing use of vehicles and machinery, high quantities of combustible materials necessarily being stored and waste’s natural ability to rise in temperature with the passage of time all add to the ‘threatscape’.
In a determined bid to unearth the key issues in play at present, we recently chatted with an insurance advisor operating in the sector. Choosing to remain anonymous, the individual concerned shared their experiences of the sector from the inside, including what’s changed, and then proceeded to outline the next steps needed.
Q: What’s the typical role of the insurer?
A: Prior to insuring a site in any sector, insurers will often sub-contract to a risk assessor or advisor. That advisor will attend the site, assess its various risks, determine if the appropriate protection measures are in place and, where necessary, make recommendations for safety improvements prior to agreeing to insure. At this point in time, the business’ safety is entirely in the hands of the insurer.
The insurer has the ability to drive up safety standards, evaluating the effectiveness of systems, ensuring they’re fit for purpose in their operating environment and providing robust advice to businesses. If an insurer’s happy, they’ll insure the site and the business will continue ‘as is’. If not, the business will need to make adjustments to the site’s safety measures in line with guidance provided by the insurer or advisor.
Q: What are the common fire safety issues you witness?
A: For the waste and recycling and waste-to-energy sectors specifically, what we tend to see is a general lack of adequate fire protection. There’s currently no legal requirement for fire protection and suppression systems to meet a certain standard or comply with particular specifications. The Environment Agency has made Fire Prevention Plans mandatory, but often these will require businesses to simply ‘install a suppression system’. They will not typically make note of the required standards or effectiveness of the system, or the conditions or environment in which the system should operate effectively.
When a business needs such a system, the decisions taken will often be driven by cost and budget. As a result, business will usually and unconsciously cut corners and opt to install a sub-standard system. This system will inevitably fail to meet their individual or operating environment risks. For example, you might be talking about an automatic fire suppression system that isn’t fit for purpose or a sprinkler system that will simply protect the warehouse shell, not the valuable equipment inside that’s essential for business continuity.
There’s also a common belief held across management that fire ‘will not happen to them’. There are so many examples of recent fires highlighting the risks, but until it happens, many businesses will only observe the bare minimum legal minimum requirements.
Q: Typically, how do insurers go about recommending products and systems to protect waste businesses against fire risk?
A: Lots of the systems insured will often come from a manufacturer’s deal. For example, a forklift could arrive fitted with a vehicle fire suppression system supplied as a bulk deal to the manufacturer. However, that suppression system isn’t necessarily fit for purpose in every operating environment and may not be effective when the vehicle is used continuously for long periods of time, with little downtime, to fulfil intense work schedules.
Some insurers will accept an insurance policy if the business has fire protection measures in place, but it doesn’t always mean they’re effective or safe in practice. Legal requirements arising from the Fire Prevention Plan will usually state that a fire protection or suppression system is required. However, it will not often stipulate that the system needs to perform to a certain standard of protection or within a certain environment.
If waste businesses are able to secure a cheaper solution and have it approved by insurers, they’ll often go down this route, trusting the system’s safety based on the fact that it’s approved by insurers. Also, many insurance underwriting templates will only stipulate ‘an approved system’ so there’s no incentive for the business to go beyond standards required to meet that approval. This is where insurers have a key part to play in driving up standards.
Q: How does your approach differ from the traditional approach?
A: Voluntary compliance and certification standards should be used to drive insurance decisions in order to safeguard sites effectively. We use two key certification standards when recommending sites for insurance approval: the FM approval standards and the SPCR (P-Mark) standard.
FM Approvals has over 200 approval standards that stipulate various criteria to ensure the effectiveness of various types of products and services. In assessing products for FM approval, a number of tests are applied to highlight products and services that meet rigorous loss prevention standards. The FM Approval certification is designed to improve and advance safety in commercial and industrial facilities. This means that any product that’s FM approved, subject to site-specific assessment and advice, can be trusted to adequately safeguard a site, giving confidence to both the business and the insurer.
When it comes to vehicle fire suppression, the SPCR (P-Mark) standard is a new global approval which has been quickly adopted as the benchmark for fire suppression for heavy vehicles and machinery. The tests are designed to evaluate suppression systems against a number of different criteria, including openness to environments, passing extensive and extreme vibration tests, environmental testing to ensure the system will operate in practice and ensuring no re-ignition of fire following system action.
Although not legally compulsory, these two standards outline a clear benchmark for any effective fire protection and suppression system for waste and recycling centres. They outline a clear route to effective fire safety for the host business, its teams and assets.
Q: What do you believe insurers need to change?
A: The onus is on the insurer to make the right decision and recommend the right systems to ensure maximum safety. A key part of that is education – educating teams, educating businesses and educating themselves as to the risks involved with cutting corners, how to prevent that scenario and how to ensure safety for each individual site being insured.
It’s the role of sales teams to be more open regarding compliance, but it’s the role of insurers to carry out due diligence to check that systems are effective enough to protect a given site. It’s a win-win scenario. Businesses will be given support and advice to feel more confident in their safety measures, understanding the importance of effective systems and what it is they’re actually paying for. With safer premises comes a decreased level of risk, lessening the chance of insurers needing to pay out as protection measures are more robust and able to withstand their operating environments.
Q: How do you feel safety regimes in the waste and recycling and waste-to-energy sectors have changed over recent years?
A: Typically, these interlinked sectors have always been prone to ‘rogue’ operations. Over the last seven years or so, though, there has been positive progression and the Environment Agency has become more heavy-handed with the implementation and enforcement of its safety legislation.
The development of Fire Prevention Plan for all sites and new permit restrictions has improved site safety. However, the sector still has a long way to go. With the help of insurers, it can move more swiftly towards maximum safety. It’s about encouraging businesses to go ‘above and beyond’ guidance and Fire Prevention Plan recommendations and doing the same ourselves.
There are a number of factors influencing risk within the sector, with several of them making the issue more pressing. These include Brexit, the implications of the Basel Convention regulations and the ongoing fall-out from China’s ban on solid waste.
Brexit is influencing almost every sector. For the waste management sectors, port disruption is already having a knock-on effect on waste storage times. For example, up until 1 January, around three million tonnes of refuse-derived fuel was sent to the European Union (EU) for combined heat and power plants. However, with post-Brexit port disruption likely to continue for some time, and with only very few UK landfills permitted to accept the fuel for disposal, sites producing it will be required to hold their waste for longer periods before it’s able to be transported or disposed of. This raises the spectre of fire risk at these sites and increasing the reliance placed on fire prevention and suppression systems.
The movement of waste between the UK and the EU is also now subject to the Basel Convention regulations, rather than just EU regulation. For businesses operating in the waste sector handling plastics, recent amendments to the Basel Convention on plastic waste mean that most plastic waste streams will now need ‘prior notification’ before shipment. There are ‘Green List’ controls which allow separated single steam plastics to move without this prior informed consent, providing agreements have been made with all non-OECD countries directly. As these agreements are not yet in place, and don’t cover all types of plastic waste, delays will likely be incurred, further stockpiling waste at recycling centres pending onward transportation. Again, this pushes recycling centres towards storage capacity, increasing associated fire risks.
Waste storage capacity is becoming a real and growing issue. It’s a juggling act between insurers and outlets. Sites are becoming more reliant on their fire suppression systems to work as the risk of fire ignition and spread increases. Such systems must operate efficiently when required to do so in order to protect business’ teams, assets and the environment.
Q: How do you see matters changing in 2021 and beyond?
A: The first point to make here is that the entire insurance market needs to be ‘singing from the same hymn sheet’. A collective approach is required.
The Environment Agency will continue looking to push fire mitigation on site, moved forward by Fire Prevention Plans. Insurers can most certainly assist in the mitigation of sub-standard fire safety systems that lure businesses into a false sense of safety by prioritising certification measures such as FM Approvals and the SPCR (P-Mark) standard.
From a fire detection perspective, it’s all about insuring the right systems. Many insurers don’t account for the specific environment of waste and recycling sites and their operating conditions’ It’s essential for them to do so. It all hinges on trust between the insurer, the business and the system installer.
James Mountain is Sales and Marketing Director at Fire Shield Systems Ltd (www.fireshieldsystemsltd.co.uk)
- “Abusive behaviour towards firefighters must stop” urges LFB Deputy Commissioner
- Surveillance Camera Commissioner and Information Commissioner sign MOU
- Cundall collaborates with ASIS
- The weakest link
- Firefighters commended for their commitment
- 2024 in Review: Transformation for Building Safety in England
- “Vital for companies to meet new standards for higher risk buildings” urges Fire Sector Federation
- MPs warn "dire consequences" of police finding
- BAFSA launches online fire sprinkler training centre
- Steve Wright elected general secretary of the Fire Brigades Union