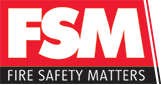
![]() |
Brian Sims
Editor |
Home> | Fire | >Suppression | >What a waste |
What a waste
11 September 2018
Recycling and waste management centres are a common place for fires, but installing automatic fire suppression systems can significantly minimise damage says Ian Gough.
FIRES IN recycling and waste management centres are a significant problem for communities, the fire and rescue service, the environment and insurers. In 2013, more than 230 fires in recycling centres were recorded - more than four per week – and of course, these are only the fires to which the fire and rescue services were called.
The problem is perhaps as much the scale of some of these fires as their frequency. A number have burnt for days and some for even weeks and have created significant logistical problems for communities. As an example, a fire at Smethwick in which 100,000 tonnes of recycled plastic was involved, required the attendance of 39 fire appliance and 200 firefighters over 200 hours of firefighting activity. The same fire consumed 14 million litres of water simply to contain it and released an estimated 19,000 tonnes of carbon into the atmosphere.
One of the problems with current UK fire legislation – and more specifically, with the fire elements of building regulations in England and Wales is that these are solely concerned with matters relating to life safety. Thus, where there is no historic evidence of fire-related fatalities or injuries, there tends to little requirement beyond ensuring that the occupants of a structures can escape safely and that neighbouring buildings are not put at risk from fire spread.
This is the same legislation that allows single storey warehouses with a 20,000m2 footprint (equivalent to approximately four soccer pitches) to be constructed without any form of automatic fire suppression systems.
Benefits of intervention
So, given people do not die or suffer injury in fires in recycling centres, it’s clear concerns about these fires can only be alleviated by the intervention of the Environment Agency or the Fire Authority for the area.
There is evidence such intervention can be effective with a prosecution in Derbyshire which resulted in the facility being closed and the manager imprisoned and barred form future employment as a director.
Perhaps the only encouraging aspects of this litany of fire and destruction are the instances where enlightened operators have taken the decision to install automatic fire suppression systems and where such systems have successfully operated and significantly minimised both the damage, the need for fire service intervention and the downtime which follows so many fires.
Deciding to install automatic fire suppression systems significantly minimises the damage, the need for fire service intervention and the downtime which follows so many fires. As with all workplaces, it is essential for the operator or owner of a recycling site to manage fire safety in a structured manner incorporating:
- Develop and issue a written fire safety policy. Effective internal mechanisms should exist to ensure that the policy is properly implemented and covers not only the normal operating regime of the location but take into account special or occasional events;
- Undertake a fire risk assessment (FRA) and review it regularly and in the event that any material fact changes - for example, if you start accepting a different class of material;
- Take steps to eliminate or reduce any hazards disclosed by the fire risk assessment;
- Ensure that a single person is made responsible for all fire safety matters and that everyone on site knows whom this is;
- Each property should compile a fire safety manual setting out its strategy and detailing its plans in case of fire and as a basis for training. Locations should also maintain a logbook to record all fire-related events such as training, drills, inspections and equipment maintenance;
- Upgrade and maintain both passive (fire separation, construction etc) and active fire safety measures (detection and suppression) as necessary;
- A systematic and effective training programme should be introduced to ensure that all staff know how to minimise fire risks, how to raise the alarm in case of fire and to provide enough trained staff to tackle incipient fires quickly. ‘Hands-on’ training with portable fire equipment (including hose reels if fitted) should be provided for any staff member who is likely to encounter a fire;
- Put in place effective precautions to manage contractors and maintenance work and in particular, to control all hot work;
- Set up regular liaison meetings with the local fire and rescue service and, in the case of larger sites, consider inviting personnel from the nearest fire stations to visit the site and familiarise themselves with its access roads, layout and equipment. Ensure that, where available, a copy of the fire and rescue service’s ‘tactical plan’ for the site is obtained and understood;
- Ensure that the risk of arson is considered and appropriate security precautions are in place to prevent intrusion; and
- Consider the need for a business continuity plan.
Fighting fires is acknowledged as a dirty and dangerous activity and fighting fires in recycling centres is no exception. Anything that facilitates a swift and effective response will provide significant benefits in terms of reducing the damage on site, reducing the environmental impact of a fire, reducing the volume of water consumed and, most importantly minimising the risk of injury to firefighters.
The most effective way of dealing with any fire is rapid intervention; to attack it in its earliest stages. Not only does this minimise the damage caused by heat and smoke but also the collateral damage caused by water. It is a well-established fact that the application of water from a sprinkler system on to a developing fire two or three minutes after it starts uses up to 90% less water than will be applied by the fire service when they arrive. Another significant benefit from early suppression is a reduction in the volume of fire water run-off which in the quantities likely from fire and rescue service intervention is an environmental threat which the Environment Agency takes seriously.
The options for firefighting equipment are:
- Portable fire extinguishers;
- Fire hose reels;
- Fixed manual systems;
- Deluge/waterspray system;
- Water monitors/cannon;
- Water mist systems; and
- Smoke ventilation
Benefits of sprinklers
Sprinkler systems will probably provide the optimum level of protection inside buildings and structures, including covering storage areas, sorting areas and provide optimum levels of protection over conveyors and hoppers. Foam additives, which can be injected into sprinkler systems may also be considered for sites accepting high volumes of plastics or other higher risk wastes. The use of foam as a wetting agent will also reduce the volume of water needed to fight a fire.
There is increasing interest in waste-derived fuel for the generation of electricity and this effectively means that some recycling centres contain small power stations - with all the hazards that implies from steam or combustion turbines, large volumes of hot lubricating oil, oil-filled transformers and rotating machinery.
It is the British Automatic Fire Sprinkler Association’s (BAFSA) view that the hazards of burning waste-derived fuels in generating plants can be countered by following the advice in BIF 25 – Fire Suppression Systems for the Waste Management Industry. And the best sources of guidance for this will be from insurers or from the US National Fire Protection Association’s Code of Practice NFPA 950:2010.4 FM Global, an international insurer also publishes useful data sheets on fire protection of turbines and related power generation equipment.
For specialist storage systems, the selection of the optimum levels of fire suppression will depend on the specific situation. For example, in the case of silos storing wood chips or pellets great care should be taken that the way in which water applied does not generate a solid mass of material which could shelter a fire generating a very dangerous situation for firefighters. Water mist or a gas inerting system may be more appropriate in such cases. This is one area where specialist advice from insurers, the fire service or other competent source of advice is essential.
Systems that generate or move large amounts of dust may need to be provided with explosion suppression systems - usually based on dry powder. Again, specialist advice should be sought in this case. Bag filtration systems and cooling towers and related plant should also be considered to be at high risk and a fire suppression provided as indicated by the FRA.
Third party certification
The utilisation of British and European (CEN) standards is essential when procuring fire protection systems. By purchasing equipment which is designed and installed in accordance with such standards, the owner of a site can demonstrate that he or she has effectively discharged any statutory duty in this respect. At the same time, utilising the services of an installer who is subject to a third party certification process and who will install equipment that has itself been tested independently and certificated will demonstrate the highest standards of care in complying with the responsibilities of a dutyholder. For more information on third party certification refer to BAFSA Information file number 20.
Note that systems being installed to satisfy UK insurers’ conditions may also have to comply with the LPC Sprinkler Rules for Automatic Sprinkler Installations which incorporate the contents of BS EN 12845 together with additional Technical Bulletins. Also note that in certain circumstances, for example, where there is a very high roof and a dry sprinkler system, the design requirements set out in BS EN 12845 for non-storage hydraulic criteria and choice of sprinkler heads might not be adequate or appropriate. In such cases, specialised insurance input is essential.
Some far-sighted and enlightened operators of recycling operations have in fact installed fire suppression systems in their plants and in 2013, successful actuations of sprinkler systems prevented serious damage to a wood pellet plant in Bridgend, recycling plants in Stockport and Shropshire and a paper recycling plant on Deeside. A major fire was averted in March 2014 in a Westbury, Wiltshire, plant. In the latter case, the fire service said, “The sprinkler system saved the day - a number of sprinkler heads were operating, containing the fire to one area”.
All of these protected plants were back in business almost immediately with little or no damage to the structures and equipment. Is it any wonder that some insurers now insist on fire suppression in recycling plants as a condition of providing insurance cover?
While recycling is an essential part of the UK’s economy and critical in enabling the country to comply with its international obligations to reduce the volume of refuse going to landfill, proper management of centres receiving, processing and converting waste is essential. Th e number of serious fires in such premises over the past five years demonstrates the need for a re-think in the design, construction and operation of such centres and this must include the provision of modern automatic fire protection and suppression systems where necessary.
Ian Gough is technical adviser at BAFSA. For more information, visit www.bafsa.org.uk