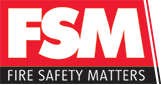
![]() |
Brian Sims
Editor |
Home> | Fire | >Suppression | >New report warns UK businesses over increase in factory fires |
New report warns UK businesses over increase in factory fires
10 December 2022
RESILINC HAS launched its global Spotlight on Factory Fires Report. The document asserts that, last year, the UK was the sixth most affected country due to an increase in the number of factory fires. Further, more alerts for factory fires were sent out globally in Q3 of this year than for the whole of 2021.

This leaves businesses in a precarious position, with over half of all fires in factories being caused by faulty equipment and machinery (59%). The second highest cause of fires was flammable liquids and gases (18%) followed by electrical lighting and equipment (10%), human error (4%), hot work/welding (3%) and combustible dust (3%).
Worryingly, of those factory fires that did start in the assembly/manufacturing area, just 11% of the buildings involved were able to activate installed sprinklers, with 9% of fires causing factory downtime of over four weeks.
When equipment and machinery is incorrectly installed, operated or maintained, fire risk continues to grow through an absence of proper safety, cleaning and maintenance procedures. A contributing factor to this is a shortage of skilled labour with employees insufficiently trained and not spotting potential risks. Other gaps around processes and component shortages are cited in the report.
The impact of these fires is significant, with 47% of them causing a medium level of damage or higher. In addition to the cost of repairs and the damage itself, there’s a substantial cost in terms of lost business and output while a given factory is non-operational. There’s also a significant impact on the supply chain. Organisations are reliant on factories impacted by fire for critical parts and goods, which those factories are then unable to fulfil.
Worrying development
“The increase in factory fires is a worrying development because of the ripple effect it causes through the whole supply chain,” observed Bindiya Vakil, founder and CEO at Resilinc.
Vakil continued: “One of the examples in our Spotlight on Factory Fires Report that really brings this home is a three-day fire that occurred at a semiconductor plant in Japan, which actually shut production lines down for six months. This sent procurement teams scrambling and the price of some chips escalated from $5 to $110 in a matter of days, ultimately costing sourcing organisations tens of millions of dollars.”
Interestingly, a supplier risk assessment later revealed that the site didn’t have automatic sprinklers or, indeed, any kind of fire suppression system installed.
“Clearly, an increase in the cost of vital parts produced by the supply chain should a supplier suddenly be unable to fulfil a client’s requirements could be hugely damaging to the client’s business,” observed Vakil. “This is where the need to map and monitor suppliers properly and on a multi-tier basis becomes crucial. Imagine if one or more businesses had identified the fire risk at the Japanese chip producer? Numerous businesses in that supply chain could have saved themselves millions of dollars in unanticipated costs.”
Resilinc recommends a combination of mapping, risk assessments and monitoring to help organisations avoid undetected fire risk in their supply chain.
*Copies of the full Spotlight on Factory Fires Report can be downloaded at https://www.resilinc.com/learning-center/white-papers-reports/factory-fires-the-top-supply-chain-disruption/
- Gallagher’s latest release hits the market
- Proposed Fire Safety Bill amendment voted down by Commons MPs
- New app promises to “transform” mandatory fire safety training in NHS
- Boost for fire safety campaigns
- Landlord of unlicensed HMO prosecuted in wake of fire safety breaches
- Check on neighbours this Electrical Fire Safety Week
- Landlord found guilty of six housing offences
- Final Call for Nominations issued by organisers of 2020 TECAs
- Fire Safety Matters and Blackhurst Budd organise digital conference on ‘Enforcing the Fire Safety Order’
- New role for former police chief of Scotland