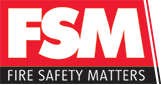
![]() |
Brian Sims
Editor |
Home> | Fire | >Alarms and Detection | >Beam Detectors: Where Do They Go From Here? |
Beam Detectors: Where Do They Go From Here?
10 July 2020
What are the benefits of today’s beam detection systems for end users? Where are these solutions commonly installed? Importantly, what’s in the pipeline for the next generation of such systems? Fire Safety Matters finds out the answers to these key questions and more in conversation with Nigel Ward.
Fire Safety Matters: What are the core benefits of beam detection systems?
Nigel Ward: The main benefit of beam detection systems is the fact that the end user can deploy them to protect an open space very cost-effectively. Perhaps any comparison with point detection-style solutions isn’t an entirely fair one because of the limitations around height, but the client would need many more point detectors to cover a given area for which they might only require a single beam detector.
To illustrate that point, we’re sometimes asked about beam detectors in corridors. One beam detector could cover, say, a 100-metre corridor, but there would be a need for 15 or so point detectors to cover the same area in addition to all of the associated cabling.
In a larger space, the end user only needs beams at opposite ends of the building. Also, there’s no defined requirement to access the middle of the building for the installation procedure. That wouldn’t be the case with an aspirating system, for example.
Roof voids might be considered as something of a niche environment, but if a beam can be aligned through the space and avoid any obstructions, it should be possible to deploy a beam detector.
There are two different technologies. There’s the end-to-end variety, whereby the beam will pass through smaller gaps (between 300-600 mm diameter), and also reflective systems. The latter require larger gaps (of 1 metre diameter) to function in the intended fashion.
Fire Safety Matters: Where are beam detectors most commonly installed?
Nigel Ward: 80% of the installations I deal with in my role are located in warehouses and distribution centres. Then there are further applications involving the likes of historic buildings, museums, aircraft hangars and airports. Sports halls are in the mix as well. In essence, as long as there’s a big open space there’s the potential for beam detectors to be installed.
The aforementioned roof voids can be problematic. They could well be pretty ‘busy’ with several obstructions. Another point to bear in mind is the potential for extreme temperature ranges. This can cause problems due to the presence of condensation. We manufacture heaters specifically to overcome this issue.
Another factor to consider would be dust. Take a paper shredding operation, for instance. In workspaces like this, very often there’s lots of dust. In this scenario, beam detectors would be in almost constant ‘fire’ mode due to the proliferation of that dust in a roof space, for instance.
Fire Safety Matters: What new products has FFE developed and launched in the last couple of years?
Nigel Ward: The most important one has been the replacement for the Fireray 50R/100R Series of reflective infrared optical beam smoke detectors which has given some really good service over the last 15 to 20 years, but they were designed a long time ago. The replacement is part of one of our new ranges of beams. It’s the Fireray One.
The Fireray One auto-aligns. Using the integrated interface, the engineer simply steers the laser on to the reflector. At the flick of a switch, it aligns itself. This solution boasts many extra features that none of our other beams currently have, but which will be incorporated into our new models. The best of those features is that Light Cancellation Technology means the Fireray One is practically immune to the effects of direct sunlight.
Fire Safety Matters: What’s the next development in beam detection for FFE after Fireray One?
Nigel Ward: Due to the impact of COVID-19 our plans have necessarily been put on hold to a degree, but next year we will be releasing a beam designed to replace the current Fireray 5,000 and Fireray 3,000 solutions. This beam will have all the benefits of the Fireray One plus a low-level controller complete with a backlight.
In a typical apex where you have three beams for coverage, at the moment we can only operate two beams per controller. Customers want three. We’ve listened to that feedback. Also, with the new system end users will be able to mix the beams. If you had, say, an area in a roof space which isn’t suitable for a reflective beam, an end-to-end beam could be added to the same controller.
In addition, it will be possible to wire them in a daisy chain configuration, in turn doing away with the traditional ‘one set of cables per beam’. The reflected beam is going to be the Fireray One detector head with all of its advantages. The end-to-end beam will have some extra features that the Fireray 3000 currently doesn’t have. The main point to note is that it will be more resistant to building movement as well as sunlight.
Fire Safety Matters: Can you tell us what else is in store in terms of the FFE product pipeline?
Nigel Ward: We’re looking to put cameras into our upcoming beam detector and flame detector ranges. False alarms in the fire industry are a massive problem. They cause unwanted evacuation of buildings, which can be extremely disruptive. Clients can also lose faith in fire safety systems if they generate constant false alarms. Further to that, the local Fire Brigade may not arrive on scene until someone has confirmed that there is indeed a fire.
The idea of putting a camera in beam and flame detector systems is all about it working like a dashcam. It will be constantly observing and recording. If there’s an activation of any kind then, 15 seconds before the activation and up to a minute or so afterwards, the footage will be uploaded to a cloud-based platform. The engineer will be able to review this footage remotely. They can see what’s happening before any visit to site. If there’s an activation, the engineer can then report to the client that it was caused by A, B or C, etc.
If we’re talking about a beam detector, the alarm could have been caused by someone placing a box in the beam’s path. Perhaps there was a cloud of dust, steam or smoke that suddenly appeared out of an operational machine. It could be that a forklift operator has put certain types of pallet on a rack at a certain height and they then interfere with the beam.
One of the issues for flame detectors is that, because they’re not aligned on to anything, they can be knocked from their intended position and the client may never notice. Also, if a production plant is re-arranged, either to maximise space or due to changing procedures, etc the flame detector will not know this. That could leave a given process at the plant with no fire protection. To avoid such a scenario, when a flame detector is commissioned a snapshot of the area it’s looking at can be ‘imaged’. When the service engineer arrives on site, they can then match up that image with what the detector is currently seeing.
If false alarms are a problem, recorded images will reveal precisely why. Cameras are definitely the way forward for beam and flame detectors. They have the potential to save on service visits to site if issues can be explained on the phone to the client and they’re then able to resolve those issues themselves as a result.
Fire Safety Matters: What major projects has FFE been involved with of late?
Nigel Ward: There are two, both of which are in the aerospace industry. The first is for the Marshall Aerospace and Defence Group based in Cambridge. The business works on military and civil aviation aircraft, the latter on behalf of operators including easyJet and Ryanair.
One of the Group’s tasks is to spray paint bespoke liveries on to the aircrafts. Paint is highly flammable, of course. In the painting booths there are a number of flame detectors. Their installation has proven to be a very positive development, so much so that the Group is now looking to expand this form of fire protection into other parts of the hangar system.
The other project is for Airbus at Getafe in Madrid where the company runs a large manufacturing plant. They make fighter and passenger aircraft. There are lots of flame detectors on site. We visited to conduct some maintenance testing as the client was a little worried about how dirty the detectors could become before they would stop functioning.
Working with the on-site Fire Department, we smeared some of the infrared detectors in grease and soil. Fire tests were conducted at a distance of 25 metres and all of the detectors were found to be working successfully.
Of course, we would never recommend a real-life scenario in which detectors are allowed to become so dirty. This would mean that a flame would need to be bigger or burn longer in order for it to be detected.
Nigel Ward is technical and customer support engineer at FFE Ltd. For more information, visit www.ffeuk.com
- Protecting our past
- Patol aspirating systems protecting your food
- From the editor
- Fire safety returns home to NEC Birmingham
- Building hope
- Blog for FSM website
- Advanced protects National Theatre
- Fire Safety Event 2017 - Live Coverage
- Advances in false-alarm management
- C-TEC rolling out CPD training events