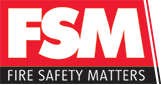
![]() |
Brian Sims
Editor |
Home> | Fire | >Evacuation | >Guiding light |
Guiding light
28 May 2022
WHEN IT comes to fire safety plans for buildings, where’s the right place to start? Is it a new build construction or a retrofit of an existing one? Whatever the scenario, each safety element has its place and a part to play. Here, Craig Stead focuses on emergency lighting and its importance in relation to overall safety and evacuation planning.

In recent years, it has become apparent that there are still many instances where installed emergency lighting is not up to the current regulatory standards, either due to the fact that the system is old, untested or even failing in some way. We know this to be true due to cases that are still being identified and the fines duly handed out by the authorities.
When is the right time to consider emergency lighting? The answer to that question is: ‘At the same time as the fire alarm system or at the point of the fire risk assessment being conducted for either new or existing buildings’.
Emergency lighting isn’t just a topic, if you like, to be considered at the end of a lighting scheme design. It’s not a ‘nice to do’ just because it’s a ‘must’, but rather an element of internal building design that, if properly planned and specified and afforded the right investment, can deliver complete peace of mind for building occupants, not to mention save resources, money and even lives.
The biggest difference – or change – that can be made right now is to upgrade existing buildings, estates and facilities, many of which are still in the ‘retrospective’ compliance arena, meaning that their management teams are continuing to present safety certificates and reports from yesteryear. What was deemed safe back in the day may not be so now.
Triggering an upgrade
Let’s take a look at some of the signs that should trigger an emergency lighting upgrade. Perhaps you’re unsure whether or not the system in your building is compliant. Maybe there’s no log of past testing/maintenance work. It could be the case that costs to manage, maintain and test your system are comparatively high and increasing over time, and notably so in view of energy price hikes. Is it becoming difficult to find replacement parts or software upgrades for your installed system given that it’s no longer supported?
Problems with your system might take forever to fix, in turn leaving that system in a state of non-compliance. Lamps and/or batteries might be an older style or technology and, therefore, need replacement on a regular basis. Is it the case that the facilities management team is struggling to stay on top of testing/maintenance requirements due to time-consuming manual processes?
Are team members unsure as to how the system works because training and support is minimal or non-existent?
If some (or perhaps all) of this sounds familiar then it’s time to make a change. Once that decision has been taken, it’s then all about the ‘what’, ‘where’ and ‘when’ of choosing and installing the right emergency lighting system such that the purchasing decisions made at the outset are the correct ones.
In terms of selecting the solution that’s right for you, every building is different. Each has its own needs and requirements with specific usage patterns, different hazards identified through the risk assessment, different types of occupant and differing maintenance regimes. One constant theme is that the need for compliance will underpin the whole process.
System design
When it comes to emergency lighting system design and its application, is the design in line with the latest standards? Are the correct lux levels being achieved? For instance, in most cases there will be a need for a minimum lux level when there’s an emergency scenario in play (ie 5 lux for Call Points, 1 lux for escape routes, 0.5 lux in open areas and higher lux levels for specific locations or high-risk task areas).
Does your scheme cover all areas stated within BS 5266-1:2016? For example, escape routes, open areas, points of emphasis (ie stairs and changes of level or direction, etc), specific locations (ie fire alarm panels and Call Points, etc) or high-risk task areas like a chemical room where additional illumination is required to either stop or completely shut down any dangerous work processes in order to allow safe evacuation and then re-occupation.
Are the products being offered, specified or installed all compliant with the latest standards? By definition, not all emergency lighting products are going to be the same. Comparing like-for-like ‘over the counter’ costs or the value engineering of a given system could be counterintuitive and invariably lead to a more costly project and higher ongoing costs. First and foremost, understanding your system objectives is essential. The choice must be made very carefully in order to satisfy compliance.
Just because emergency lighting system specifications may look identical on paper doesn’t mean to say that they are. Think about performance characteristics. Some systems allow for fittings to be installed every six metres along an escape route, while others that look identical could be focused on a spacing of every 24 metres or more.
Don’t be fooled by the stated lumen output of an emergency luminaire, either. This isn’t the correct ‘benchmark’ by which to check a luminaire’s performance as light distribution can be optically controlled.
Batteries and testing
Did you know that there are self-contained emergency luminaries where batteries can last for longer than 12 years? Such systems result in lower maintenance activity, reduced costs and a huge reduction in carbon footprint (of between 30% and 80%, in fact) if you’re using the right one.
What about mains conversions (ie converting mains-driven luminaires to an emergency lighting set-up)? With the advancements in optical control, mains conversions are now one of the least efficient ways in which to deliver compliance. More often than not, luminaire conversion will result in unnecessarily increased and costly product requirements in order to achieve the same goal that would have been realised with a stand-alone system.
Are you conducting your testing regime diligently and, importantly, in line with the current standards? Testing, monitoring, maintenance and reporting of an emergency lighting system is mandatory. In order to meet compliance regulations, the minimum test requirement for emergency lighting is that each emergency luminaire is functionally tested every month. In point of fact, you should visually check the system on a daily basis if a central battery unit is being used.
Once every year, the entire system needs a full discharge and a complete operational test. The system must still be capable of illumination at the end of that period and correctly switch back to re-charge. Testing guidance is afforded within the pages of BS EN 50172.
Predominantly, testing is an ‘out of hours’ task. There are now testing systems available to help achieve regulatory compliance. Self-test fittings will test automatically, but there’s still a requirement to visit each fitting every month and check and record the results. Testing systems such as the Clevertest Plus are supplied with a free of charge app for the Android and iOS platforms. The app acts as a logbook for many sites with reports available at any time.
Auto-test or addressable testing systems are now available using SMART, wireless and RF technology that goes beyond compliance. The Zoneworks XT HIVE, for example, can control 1,000 emergency luminaires connected wirelessly to just a single controller with no need for extra wiring or any wired devices like boosters or repeaters.
Thanks to remote connectivity, the end user can view the status of their emergency lighting system for an entire estate (ie an unlimited number of buildings) within a matter of seconds and then create maintenance and test reports at the touch of a button.
Maintenance regime
Are you maintaining your emergency lighting system to ensure continued compliance? To meet the compliance regulations, you need to prove that you actively maintain your emergency lighting system. Using longer-life products with longer-life batteries will help to achieve compliance with very little – if any – maintenance being required for that aforementioned period of 12 years or more.
If maintaining compliance for longer with less effort is what’s needed, your battery choice is absolutely critical, as are warranties from quality manufacturers. Not properly addressing this issue is one of the biggest mistakes that can be made.
Are you completing regular risk assessments? Are you aware that there’s a need for a regular risk assessment to ensure your building is safe and compliant with the Regulatory Reform (Fire Safety) Order 2005? This process will help to pinpoint areas where there are compliance issues such that they can be rectified. Simply relying on an old fire certificate is no longer acceptable. Any lack of a risk assessment could lead to a fire safety audit failure and the potential for fines to be issued by the courts.
One of the main components of an emergency lighting system is signage, which should be considered at the very beginning of your design/specification process. It’s obligatory to ensure that escape routes are clearly defined and identified with the correct exit signage.
When selecting a product, be aware that the calculation for the viewing distance of an internally illuminated exit sign is 200 times the height of the sign (ie an internally illuminated sign with a height of 100 mm would realise a 20-metre viewing distance).
Externally illuminated signs, including Photoluminescent exit signs, are an option for the system design, but the viewing distance is only 100 times the height of the sign, which is half that of an externally illuminated sign of the same size. They need to be illuminated to 100 lux in a mains healthy condition and 5 lux in an emergency condition.
In addition to this, they must have an emergency luminaire within two metres on the horizontal plane.
Don’t risk compliance
Emergency lighting is a legal requirement that needs to be understood, embraced and, ultimately, taken very seriously indeed. The regulations, processes, technology, systems and solutions are readily available now to support a safer and more sustainable built environment.
For the practising end user, embarking on the task of finding a system manufacturer partner that can help to guide you through the whole process of system selection, specification and installation is highly recommended.
It’s time to stop paying high maintenance costs and stop risking compliance as a result of carrying on with older, non-performing emergency lighting systems. No matter how big or small your building, there’s a new system out there that will suit your needs, save you money and, most importantly of all, protect and safeguard lives should there be an emergency episode.
Craig Stead is Country Manager (UK) at Clevertronics (www.clevertronics.co.uk)