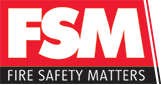
![]() |
Brian Sims
Editor |
Home> | Fire | >Manufacturing | >Fire Product Supply and Demand: Mitigating the ‘Bullwhip Effect’ and the ‘Snowball Effect’ |
Fire Product Supply and Demand: Mitigating the ‘Bullwhip Effect’ and the ‘Snowball Effect’
30 August 2022
SINCE THE beginning of the year, it has been noticeable that the supply of various technologies – including fire detection systems – has become more and more difficult to orchestrate. Gordon Thomas examines the global shortfall of raw materials and finished products impacting the fire sector and what’s being done to mitigate this issue.

Let’s start by looking at those market effects behind this global shortage of raw materials and finished products. The two that have come into play are known as the ‘bullwhip effect’ and the ‘snowball effect’. The former occurs when a shift in demand impacts previous forecasts. Changes fluctuate rapidly, in turn creating a ripple effect along the supply chain, which can be likened to the movement of a whip passing through the air and ‘cracking’.
The ‘snowball effect’ is perhaps best likened to a scene from Fawlty Towers. A small and seemingly insignificant issue occurs which then rapidly escalates with other small issues. Each compounds the other until such point that the end result is too difficult to overcome. Much like rolling a snowball down a hill, that snowball gains momentum and can be out of control very quickly.
In terms of technology products like fire safety systems, there are several global supply issues affecting raw materials and components. Let’s just focus on one of them, though: semiconductors.
At the core
Semiconductors are at the core of every technology product in existence. The semiconductor market has witnessed supply issues due to external forces and suffered from the bullwhip effect in the change in demand by consumers during the start of the COVID-19 pandemic. It’s not all down to COVID, though. Effects occurring alongside the impact of the virus also contributed to the ‘snowball effect’.
In September 2020, the US-China trade war began with the Trump administration-imposed restrictions on China’s largest chip manufacturer. The restrictions placed here by the US Department of Commerce made it extremely difficult for the Chinese chip manufacturer to supply chips to any company with American ties. It was a move that resonated with other Governments around the world and they too began to bring forward similar restrictions (both explicit and implied in nature).
For their part, manufacturers were forced into souring semiconductors from other manufacturing plants in places like Taiwan, Japan, central Europe and America. These other semiconductor producers then began to see demand exceeding their manufacturing capacities.
When COVID hit hard, consumer demand changed from components used in industries such as fire and security, the automotive sector and building management, etc. Projects and needs for these technologies declined in part due to the rapid increase in the need for more computing power, network infrastructure and telecoms to adjust for the rise in working from home following the onset of the pandemic.
Environmental impacts
In February last year, a severe winter storm battered Austin, Texas and forced the closure of two semiconductor manufacturing plants due to the loss of electrical power supplies, which impacted them for several months.
Also in 2021, Taiwan recorded its worst drought in the last 50 years. The production of semiconductors requires vast amounts of pure and ultra-clean water. One manufacturing plant alone would require 63,000 tonnes of water per day, which simply wasn’t available.
Fire outbreaks in Germany and Japan closed down the production of not only semiconductors, but also the lithography equipment used in chip manufacture.
The ongoing Russia-Ukraine conflict is also an ongoing factor to consider as Russia is one of the largest exporters of raw materials such as neon and metal palladium. Ukraine is a leading supplier of Krypton and Xenon.
With the Western world placing trade restrictions on Russia, global chip manufacturers are forced to look elsewhere for these raw materials. Delivery will take time to ramp up (as defined in the ‘bullwhip effect’).
Mitigating the problem
The supply and demand versus price ratio has also kicked in with the difficulties in obtaining raw materials, forcing price increases of said materials through the roof in some instances. Manufacturers have had to resort to ‘spot’ buying, purchasing at higher rates than the norm. Eventually, such cost must be passed on.
Fuel and energy costs have risen over the last few months. That being so, the cost of production and transporting the goods at both the components and finished goods stages has massively increased.
Manufacturers have had to overcome these supply and demand issues. Several techniques have been deployed. There has been the re-engineering of finished products to allow more resilience in alternative components. Surcharges have been brought in to cater for pricing variations. Further, we’ve seen the inevitable price increase in order to sustain production capability.
These price increases and delays in availability pass along the supply chain such that integrators, distributors and end users/contractors need to adapt practices to prevent the ‘snowball effect’ from impacting companies’ profitability and the delivery of projects needed to stabilise the global shortage.
Some simple strategies such as sticking with the original supplier, providing better long-term forecasts and building resilience for projects in delivery times, not to mention removing penalties for late delivery, all help to prevent the ‘snowball effect’ from having a major impact on the back end of the supply chain.
When will it all end?
When will we see an end to these production shortages? Industry analysts are predicting the impact on the global market will be with us until at least mid-2023. Micro changes have been made by manufacturers to counteract the impacts, but the next stage is going to be crucial.
Gradually, we will see supply lines improve following the changes manufacturers have implemented, but to prevent the ‘snowball effect’ further down the supply chain, integrators/distributors and end users need to reflect on the impacts their actions will have on the ultimate stabilisation of the global shortage.
Stick with the original supply channel. Swapping to alternatives is how the ‘bullwhip effect’ starts. Contractors and end users need to be aware that the integrators and distributors are not at fault here. Penalising them contractually for late delivery is just going to drive the behaviour that energises the ‘bullwhip effect’ in the first place.
An alternative solution that benefits all parties is to plan earlier. Allowing partial shipments of components when they are available will help to reduce the burden a single delivery may exert on the ability to supply.
Gordon Thomas is Business Development Manager for Global Fire Detection Products at Johnson Controls (www.johnsoncontrols.com/en-gb)
- BAFE resumes fire extinguisher technician assessments and BS 5306 exam invigilation
- New lead expected for undercover inquiry
- LFB unveils new equipment
- Fire and Rescue Services stress pandemic is “no excuse for ignoring fire safety”
- Partnership to fight economic crime
- Survey reveals half of police officers willing to be armed
- BRIGADE WELCOMES ROGUE LANDLORD DATABASE SUPPORT
- IQ Verify audits HX Car Park Management Ltd for certification against Surveillance Camera Code of Practice
- Former BAFE CEO receives prestigious Lifetime Achievement Award
- Prisons project gathers pace