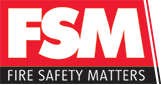
![]() |
Brian Sims
Editor |
Home> | Fire | >Alarms and Detection | >Going to the next level |
Going to the next level
04 November 2017
Stephen Beadle examines what role new solutions can play in helping make every detector testable.
ADVANCES IN detection, building design and regulations mean that the challenge of achieving compliant testing of detectors is constantly evolving. In some cases, the siting of detectors makes them hard-to-access and in other cases it’s the type of detector that can prove the challenge. These factors, on top of an increase in companies looking to achieve 100% compliant testing, means there is a need for the test solutions to constantly evolve. By doing this the goal of 100% compliant testing becomes closer to reality.
For many years the only approved method for carrying out a functional test of a smoke detector was with the use of a pressurised smoke aerosol can. Offering a reliable, universal solution to the challenge of smoke detector testing, the method has been widely adopted by maintenance companies world-wide.
The reign of the smoke aerosol can has been challenged in recent years by regulations and also the emergence of cartridge-based solutions offering greener, faster and safer testing. Despite these advances, aerosol cans are so well established and have such a strong reputation, that they have remained the most popular solution for fire engineers worldwide.
The latest regulation change affecting the use of pressurised aerosols is designed to remove products containing hydrofluorocarbons (HFC) gases from the market. This means that as of 31 December 2017, the industry leading Solo smoke aerosol offering will be changing - with Solo A3 no longer manufactured.
Rather than signalling the end of smoke aerosols, this milestone is actually providing the market with greater choice – with Solo A10 as a replacement for the non-flammable Solo A3, and Solo A5 as a flammable alternative. As with all Solo products, these new smoke aerosol cans are approved by third parties and leading detector manufacturers. They both offer comparable performance with the Solo A3 and are fully compatible with the Solo dispense.
Non-pressurised smoke generation
Some users have made the move to non-pressurised smoke and this latest regulation change has led to more taking the opportunity to move to cartridge-based smoke. Some of the latest detector designs have also proved hard to activate with a traditional smoke aerosol can. The smoke generated by cartridge-based solutions tackles this by offering a realistic smoke compatible with the widest range of detectors. As well as operational benefits, a big advantage of cartridges is the fact they are classified as non-hazardous, which means they can be shipped and stored much easier than pressurised alternatives. They typically support on-demand generation, which means smoke is only generated when the tester is placed over the detector and eliminates the risk of over-application that can lead to detector contamination and repeat alarms.
The recently launched Solo 365 has proved an instant hit with early users. Many have taken to the new technology as a way of future-proofing their testing – ensuring compatibility with the widest range of detectors and avoiding any possible further regulations which may affect pressurised aerosols.
In terms of the types of detector now being used, the market is now seeing far more multi-sensors – particularly in new builds. These detectors, of course, present another challenge, with multiple sensors requiring testing, and in some case all sensors being tested simultaneously. Such developments have led to wider use of an all-in-one detector tester, which offers the ability to test smoke, heat and CO from one device. Naturally, use of one tool for multiple functions brings about productivity savings – with engineers having less to carry around site and spending less time switching between testers.
British Standards update
The recent update to BS:5839-1 has also, for the first time, placed a focus on how multi-sensors should be tested. In 45.4(j) sub-clause 2 It now states: “multi-sensor fire detectors should be physically tested by a method that confirms that products of combustion in the vicinity of the detector can reach the sensors and that the appropriate response is confirmed at the CIE.”
Testing all sensors within a multi-sensor could lead to an increase in testing time. This helps maintain fast and effective testing while providing a reliable, approved method of ensuring all sensors are able to detect fire and enter alarm in the event of a real-life fire situation. Single stimulus testing of smoke, heat and CO is also possible, making these testing solutions as suitable for single sensor detectors and it is multi-sensor detectors.
Carrying an all-in-one tester also ensures the engineer has a solution for every type of detector on site whether that is a smoke, heat, CO or multi-sensor. A built-in ‘clearing mode’ within the tester supports faster testing – clearing the area around the detector of any remaining stimulus and therefore preventing repeat alarms after initial testing.
Another update to the standard is the recognition that while the majority of detectors can be easily accessed, there are some detectors that are sited in hard-to-access locations, which of course should also be tested. Clause 22.1 state: “For remotely situated or hard-to-access detection equipment, consideration needs to be given to the feasibility of testing and maintenance at the design stage.”
The modern design of buildings has seen greater creativity in design, with many voids and large open areas – all of which have a form of detection in and all of which need to be tested. Other common areas of hard to access detection include lift shafts and secure rooms – again, detection installed here needs to be tested. Often this is at great expense, involving third party engineers, extra staff and increased disruption.
This has led to advances in the test solutions available as the market looks to reduce the cost of maintaining such detectors whilst still achieving 100 percent compliance. The availability of a tester, which is permanently installed alongside such hard-to-access detectors means detectors in lift shafts, ceiling voids, secure rooms and other hard-to-access locations are now easily tested at the same as easy to access detectors – without the need for additional personnel and cost.
Testing ASD systems
The testing of aspirating smoke detection systems is another challenge faced by engineers. Historically, there have been different methods used for testing with varying levels of reliability and accuracy achieved. Our Scorpion solution, as well as being suitable for hard-to-access smoke detectors, is also designed for use with ASD systems fitting directly to the pipe, either at the end of the run or close to a sampling hole. Testing is then easily carried out via a connected access point housed in a more accessible and convenient location.
While this, permanently installed solution, can be retro-fitted there are times when this isn’t practical. For these situations and where access is possible, a more portable solution exists in the form of an ASD adaptor. A simple solution, the adaptor is carried by the engineer and simply fitted to the tester in place of the clear cup that is used for testing of point detectors. The adaptor fits neatly around the pipe and delivers smoke into the sampling hole, along the pipe and back to the panel – ensuring the system is functioning and able to detect the presence of smoke.
Mobile engineers
The type of sites engineers are required to maintain and the locations they work in are also changing. An increase in engineers permanently assigned to a particular site and also those who are working without a vehicle in built up areas has led to enquiries for a more ‘mobile’ test solution.
This situation has led to the creation of portable test kits, which include shorter versions of access poles carried in a compact rucksack. The rucksack includes space for all the essential tools required for testing and maintaining fire systems and additional accessories such as laptops and hand-tools.
The shorter versions of the telescopic access poles support quicker movement in and around site and when travelling on public transport. They are generally lighter than the traditional test kits and help reduce disruption when moving around sites.
With regulations, technology and design continuing to develop at an increasingly rapid rate, the challenges faced by fire engineers when testing detectors continue to increase. Whether it’s the testing of a detector in a modern new building with high ceilings or the need to test a series of multi-sensor detectors on a number of inner city sites – it’s important that solutions are provided to make these tasks faster, safer and easier.
Stephen Beadle is marcoms manager at Detectortesters. For more information, visit www.detectortesters.com
- Detectortesters Group moves to acquire Minneapolis-based Global Vision Inc
- Detectortesters heralds acquisition of The Hose Monster Company
- Detectortesters wins third prestigious Queen’s Award for Enterprise
- Scorpion installed at Southampton University
- Open for business
- Detectortesters Solo at Fire Safety Event
- Detectortesters training moves online
- The high test
- Detectortesters set to share research
- The Hose Monster Company introduces In-Line Pitotless Nozzle to UK market
- Protecting our past
- Patol aspirating systems protecting your food
- From the editor
- Fire safety returns home to NEC Birmingham
- Building hope
- Blog for FSM website
- Advanced protects National Theatre
- Fire Safety Event 2017 - Live Coverage
- Advances in false-alarm management
- C-TEC rolling out CPD training events