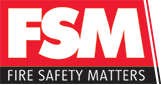
![]() |
Brian Sims
Editor |
Home> | Facilities | >Health and Safety | >Risk matters - October 2018 |
Risk matters - October 2018
14 September 2018
With a low-skilled and multi-cultural workforce at the heart of the UK’s recycling and waste sector, Jacqueline O’Donovan discusses why it’s crucial that companies go that extra mile when it comes to engagement and training.
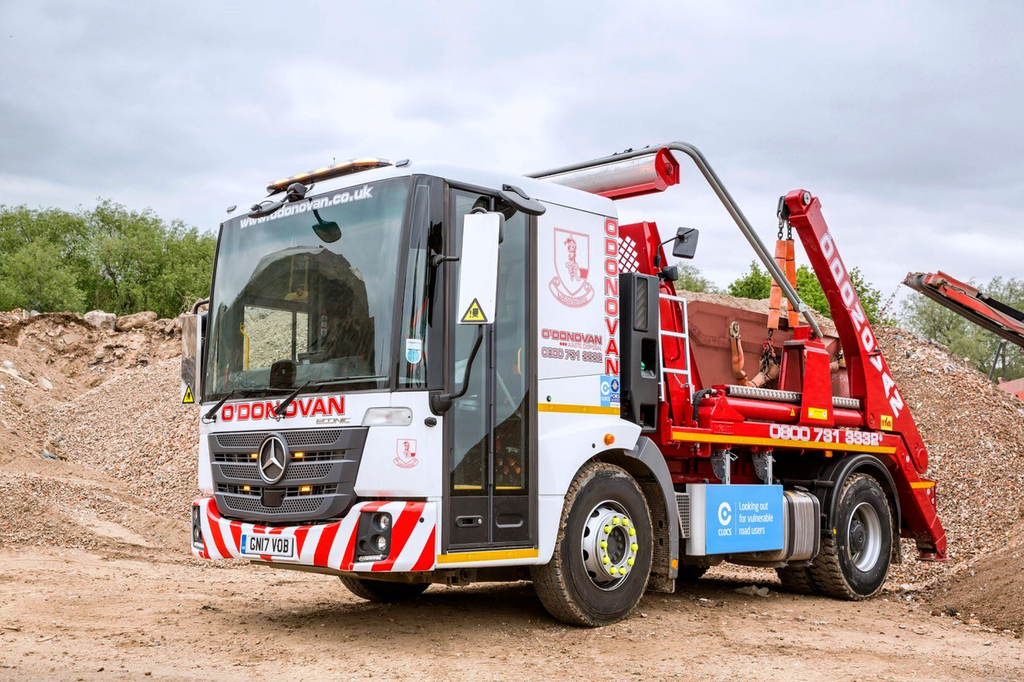
THE WASTE sector in which we work, is amongst the most risky industries according to the Health and Safety Executive (HSE). In its report Workplace Fatal Injuries in Great Britain 2018, the HSE said the number of fatalities per 100,000 workers employed showed waste on 10.26 with a five-year average of 7.22. This was ahead of both agriculture at 8.44 (8.20 over five years) and construction (1.64 and 1.77).
Although there has been a constant focus across the industry for a number of years now to improve safety, there’s still a way to go. I believe that the crucial key is training and education up and down the operational hierarchy, no matter the skill level of the job description.
With this in mind, it is vital that businesses in the sector develop strategies and set aside investment to educate and upskill staff, so they better understand the risk connected to their working environment and to ensure their safety and that of their colleagues. With multi-lingual workforces more commonplace in the UK, having a comprehensive and robust training plan that takes differing languages into account is important. Take our own operations as an example, across the 160-strong team at O’Donovan there are currently eleven different nationalities and, for the majority, English is their second language.
As an employer, we need to be confident that those with English as a second language are able to fully understand the importance of the messages being delivered, whether verbally or in writing.
The importance of training and education to any business cannot be overstated and should not be underestimated. Take, as an example the waste picking line where training isn’t commonplace, yet improved knowledge can have an important bearing on the bottom line. Conventionally in the waste industry, the only training a waste handler would receive is a short induction process on how to do the job, as well as the health and safety and operational aspects of the role – all of which is normally done as a new starter.
Ongoing training
Additional and job specific ongoing training not only improves safety, it also improves cost-effectiveness, with pickers adding substantial value by knowing the reasons and understanding the multitude of waste streams and being able to improve recovery rates and the overall quality of the material - therefore assisting the overall goal of the circular economy. This in turns assists the company in having a safer and more efficient environment to work in, as well as a better bottom line.
Over the years, we have put in excess of 60 members of the team through NVQ Level 2 & 3 Waste Management Industry Training and Advisor Board (WAMITAB) training courses. Given the cultural mix of our team, we also ran the courses in a multi-lingual format, which meant that we could be confident that the importance of the information being conveyed was fully appreciated – and not lost or lessened in translation.
Not only did these courses provide our staff with the most up to date training so they were able to safely undertake the removal of all wastes in a safe manner, they also focused on maintaining the highest quality of material, and safety standards while carrying out their job. As a result, we’ve seen greater staff knowledge of waste streams, further improving material quality and productivity and increasing staff engagement which results in us as a company being more sustainable as a business. The improvements have in turn seen a reduction in insurance premiums.
The investment by O’Donovan has allowed us to educate those who would not normally be given formal training and the opportunity to upskill – something that we see as a cornerstone of the business. Offering training to the team has also provided us with the opportunity to show our commitment to their education and in turn has made them feel valued and engaged in the business.
Health and safety is a lot more than adhering to regulations or ticking a box as it has a huge impact on people’s lives, gives our staff the knowledge to operate at the safest levels and is vital to the efficient running of our business. Training may be a large investment in a company’s time but is invaluable on so many levels, and I wholeheartedly standby this statement. Other waste operators should take on board the overall savings that training has had, in particular the insurance savings which far outweigh the training costs or time. To introduce training is relatively simple and can be un-complicated – if, as I say, you just “keep it simple”.
For O’Donovan, it has made staff feel inclusive and the consistent education of the whole team has made us stronger and safer as a business and has also seen our staff retention rates improve which had contributed to our continued success.
Jacqueline O’Donovan is managing director of O’Donovan Waste Disposal