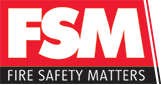
![]() |
Brian Sims
Editor |
Home> | Fire | >Manufacturing | >Fire Safety: Choosing a Ventilation System Supplier |
Fire Safety: Choosing a Ventilation System Supplier
14 May 2024
IN THE construction industry, selecting the right ventilation system supplier is paramount to any project’s success and efficiency. The decision-making process involves a thorough evaluation, from ensuring compliance with industry standards to addressing specific needs. Here, David Fitzpatrick delves into not-so-obvious questions worth asking before entering into co-operation agreements.

We often begin by asking questions that may seem straightforward. We typically evaluate the quality, pricing and risks associated with initiating a new collaboration. However, there may be instances where we don’t have ample time to choose. Alternatively, we may come across products that claim to be “innovative, low-priced and of very high quality”, but what exactly do these claims mean? Questions need to be asked and answered.
- How long has the supplier been in business and what is their track record?
- What specific experience does the supplier have with ventilation systems in my application?
- Can the supplier provide detailed technical documentation, data sheets nd drawings?
- What’s the lead time for delivery of ventilation systems and how does it align with my own project timelines?
- What level of customisation or flexibility does the supplier offer to tailor systems to my specific needs?
- Are there any ongoing maintenance or support services provided after installation?
- What certifications or standards does the supplier’s ventilation system(s) meet?
- What’s the supplier’s approach to quality control and assurance throughout the manufacturing process?
- How does the supplier handle potential issues or challenges that may arise during installation or operation?
- What’s the total cost of ownership for the ventilation system(s), including installation, maintenance and energy consumption?
Next steps
The above questions are a reminder of what you probably already knew. The following are based on more specific aspects that significantly differentiate suppliers in the marketplace. Check what can make them stand out besides quality and pricing.
Fully-tested ventilation system
- Are all components rigorously tested and quality-controlled by the manufacturer?
- Is there an in-house manufacturing process to ensure thorough testing and quality?
- Has the system been tested as a whole with all of the products integrated?
- Did third party companies confirm certification?
Ensuring that all components are rigorously tested and quality-controlled is essential to guarantee the reliability and performance of the ventilation system. Inquiring about the manufacturer’s production line, testing processes and third party certifications helps to verify the system’s compliance with industry standards and its ability to function effectively in real-world conditions.
It’s always important to remember that products may behave differently when tested individually as opposed to when they’re part of a system.
Transparent design concept
- Is access to the complete design concept provided upfront, including mathematical data, research findings and CFD simulations?
- How quickly will you receive the initial project proposal?
- What additional costs are associated with support?
- Is transparency maintained throughout the educational support to the client instead of fostering a culture of smoke and mirrors?
Flexibility in space shaping is pivotal to remain competitive in the construction market. Rearrangement affects fire scenarios and the hydraulic properties of the building. Ventilation suppliers may use sub-contractors for design. The time and scope of support may vary, with additional charges for each extra action.
However, a project should include air volume calculations, equipment selection, device and shaft locations, unusual scenarios or architecture considerations, not to mention proof of efficiency via CFD simulations.
Intelligent control system
- How effectively does the ventilation system manage stack effect challenges in high-rise buildings?
- Are there any control systems in place to ensure speed of response and reliability?
Wind pressure against the building affects internal pressure, while temperature-driven air density differences create air movement in high spaces, causing uneven pressure. A building’s airtightness degrades over time, necessitating manual recalibration of passive mechanical systems. As such, it’s crucial to understand how the system operates under changing conditions.
Client choice in installation
- Is there flexibility in choosing the specialist contractor for system installation?
- Have recommended contractors been trained and already worked on the products they will install?
- Will you receive support from the manufacturer’s engineers who developed the units?
Properly designed systems can face installation issues, leading to device malfunction, building rejection, system inefficiencies, security risks and warranty problems. Minimising failure risk is crucial for long-term systems that are meant to save lives. Hiring experienced installers trained and familiar with the products they will install is an investment in safety and ensures proper compliance with manufacturer specifications.
Daily system monitoring (notably for pressurisation systems)
- Is there a commitment to ongoing maintenance and monitoring beyond installation?
- How is system performance ensured daily for longevity and peace of mind?
Automated systems should monitor all components of the pressurisation systems and automatically test the dampers and fans every 24 hours. As the building ages, its airtightness may degrade due to ageing seals or new installation holes, requiring manual recalibration of passive systems, which can create maintenance challenges. Therefore, a system with 24/7 control and automatic adaptation to current conditions is preferable. Daily system monitoring helps to detect and address potential issues promptly, thereby minimising downtime and operational disruptions.
Well-informed decisions
By asking these comprehensive questions, stakeholders can make well-informed decisions when selecting a ventilation system supplier. Prioritising reliability, transparency and ongoing support ensures ventilation systems’ successful implementation and operation in diverse construction projects.
David Fitzpatrick is General Manager for UK Operations at SMAY Ventilation Systems (www.smay.pl/en/)
*For additional HVAC guidance, send an e-mail to [email protected]