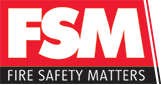
![]() |
Brian Sims
Editor |
Safety first - October 2018 | 24/09/2018 |
---|---|
The British Industry Safety Federation (BSIF) manages a number of product specific special interest groups where its members can meet and discuss any issues related to their products, and to learn news from the standards and regulatory world which may affect them, explains Frank Angear. ONE OF these Groups concentrates on Respiratory Protective Equipment (RPE). The BSIF Respiratory Protection Product Group is a ‘broad church’. It was, like many more of BSIF’s product groups, born out of the original Personal Safety Manufacturers Association (PSMA) group for manufacturers of RPE. However the lines which define a manufacturer have become increasingly blurred in recent years due to:
Because of this, membership of the Respiratory Protection Product Group in recent years has grown to include RPE importers with manufacturer’s responsibilities, brand owners, and distributors, and during last year the Group further expanded to include organisations with specific interest in RPE in such areas as specialist industry distribution, and provision of fit testing. The Group collectively is keen to ensure the needs of new members are also met, and to find the most appropriate way to serve their interests so that their work and outcomes can reach the widest audience within their area of respiratory protection. Add to this standing invitations to participate to a number of other stakeholders, including the Health & Safety Executive (HSE), the Health & Safety Laboratory, and Notified Bodies who issue certification for RPE, and you can see just how broad the agenda can be. British Standards BSIF nominate a number of individuals from this Product Group to sit on the UK’s national standards committee at BSI. Through this work they can also represent the UK at CEN committees in Europe and at ISO Standards drafting meetings globally, and these activities are reported back to those attending each Group meeting, keeping UK manufacturers up to date with developments in the regulatory aspects of their business. This is particularly of interest at the moment as a number of supporting ISO standards on test methods and other aspects of RPE requirements have recently reached publication stage, and we are getting very close to the publication of the main two ISO performance standards, one for supplied air RPE and the other for filtering RPE. In addition, 2017 and 2018 has seen work progress at CEN as all the EN RPE standards have become due for review, and many will have revised editions published. These will follow the approaches adopted by ISO in their work on global standards, so that transition between the two and the development of product to meet both sets of requirements will be feasible. The HSE play an active role in most of the BSIF special interest groups, but it has always worked particularly closely with the Respiratory Protection Group. The BSIF also administer the Fit2Fit scheme which accredits individuals, provided they can pass a stringent written and practical examination, as competent to conduct fit testing, and the HSE are heavily involved in maintaining the operation of this scheme. Over the last two years the HSE guidance on fit testing, OC 282/28, has been revised, and from its new publication date much of the guidance will be provided by ‘industry’ in the form of an accompanying document produced by the BSIF. From now on HSE will prescribe ‘what’ you need to do to comply, and Fit2Fit will explain ‘how’ you can do it. Finally, I cannot complete this review without paying tribute to the Group’s most recent past Chairman, Alan McArthur of 3M. Alan had guided this Group unerringly for many years before his untimely death early this year. Many will remember him through other avenues as he was deeply involved in his subject over a wide variety of ways in providing assistance on RPE matters, and certainly proved to be a fountain of knowledge on the subject, but those associated with the BSIF and the Fit2Fit scheme will remember him for the great contributions he made to their development and continuance. The Group is in equally safe hands now with a new Chairman, but few will forget the legacy that Alan has left us. Frank Angear is general manager of the BSIF. For more information, visit www.bsif.co.uk |
|
|
|
Safety first - September 2018 | 25/07/2018 |
A new standard has been specifically designed to provide guidance on how to conduct a fit testing of tight-fitting Respiratory Protective Devices (RPS), says Alan Murray. WHEN SPECIFYING Respiratory Protective Equipment (RPE) which includes Respiratory Protective Devices (RPD) it is important to consider the role of Fit2Fit and the needs of the user in addition to the performance characteristics of the RPE. The importance of protecting workers from hazardous dust and fumes is not a new topic of debate. For some 2,000 years, the potential dangers have been recognised. Fast forward to the present day and the issue remains a hot topic for debate and a key area of international safety legislation. So much so that 2018 has seen the introduction of the ISO 16975-3:2017 – a new standard specifically designed to provide guidance on how to conduct a fit testing of tight-fitting Respiratory Protective Devices (RPS) Designed to evaluate the effectiveness of the seal between the wearer’s face and the respiratory interface specific requirements for conducting RPD fit testing outlined in the new standard include:
We need to drive mindsets away from pure respirator performance to the relationship between respirator and each individual user. In the past a lot of disposable respirators were introduced to the market to purely meet the EN 149:2001+A1:2009 standard, without necessarily considering the individuality of the user, how it fitted them and how it was used. If someone fits a particular disposable FFP3 mask – that would then apply to any FFP3 mask product – These are assumptions that are being made – WRONG! It is important to reinforce the message that if a respirator model is changed then the wearer needs to undergo a new fit test. Fit testing Where a tight-fitting face mask is required, a fit test on that mask and the person wearing it needs to be carried out. This is a legal requirement detailed in the CoSHH regulations. Some people still don’t understand whether fit testing is a requirement for them or don’t know enough about it to make an effective judgement. Fit testing is also seen by some as time consuming, expensive or not applicable to them e.g.: ‘I only wear a mask once a week, so its OTT and not needed’. Regardless of how often a mask is used – if it’s being used as an item of PPE it needs proper fit testing. It's also recommendable that regular fit testing is undertaken – ideally at least once every two years. Recent research indicates that up to 50 percent of all RPE used does not offer the wearer the level of protection assumed and one of the major reasons is that it simply does not fit! Yet, under the regulations RPE must be correctly selected and this includes, for many types of RPE, a face piece Fit Test conducted by a competent person. So how can you be sure the person conducting the fit test is competent? Despite not being qualified to do so, some people think they are competent enough to fit test. RPE fit testing should be conducted by a competent person, anyone carrying out the fit test must be appropriately trained, qualified and experienced. In view of these major concerns the British Safety Industry Federation, along with the HSE and other industry stakeholders have developed a competency scheme for Fit Test Providers. The Fit2Fit RPE Fit Test Providers Accreditation Scheme is designed to confirm the competency of any person performing face piece fit testing. What makes a Fit2Fit accredited tester competent? They have passed an industry recognised exam and therefore demonstrated they have a thorough knowledge of the HSE guidance on fit testing and can demonstrate they have the know how to fit test in practical circumstances. If you or your employees require a fit test, then by using a Fit2Fit accredited tester you will be doing enough to demonstrate best practice and making sure the user of RPE is properly protected and has an effective seal on their mask. A list of accredited, competent fit testers can be found by going to www.fit2fit.org and clicking on the ‘Find a tester’ tab. Why take the risk of using a non-accredited tester when it’s so easy to source a fit test from a competent Fit2Fit tester? Alan Murray is chief executive of the British Safety Industry Federation. For more information, visit www.bsif.co.uk |
|
|
|
Safety first - June 2018 | 01/05/2018 |
Alan Murray warns of the dangers of failing to ensure that hazardous and combustible substances are properly stored. IN MOST laboratories and industries, the use of hazardous and combustible materials is part of the regular routine and is unavoidable. On a daily basis the improper storage of such materials puts people, the environment and property in danger. A worst case scenario, such as the one described in the following example, could happen to anyone. As a result of a minor accident in a laboratory or industrial premises, a small fire breaks out. Quantities of flammable material stored incorrectly on a shelf quickly accelerate the speed of the fire. In this instance, evacuation times and fire extinguishing times are reduced, resulting in potential injury and damage to the premises. In such cases, the negligent handling and storage of hazardous materials has serious consequences. The general lack of safety measures, along with the failure to mitigate the risk of fire spread, could possibly lead to insurance issues. Additionally, the laboratory manager and safety manager could face prosecution, and the personal liability of the company’s senior management may be involved. Substantial costs for disposal and renovation would arise and incalculable production losses would ensue. Furthermore, the associated damage to the company’s reputation could have potential long-term effects. Hazardous materials are therefore always very much a current topic for every business. In order to avoid accidents and to protect employees in the best possible way, hazardous materials must be stored in the correct way, for example in a safety storage cabinet. Particularly strict storage regulations concerning the handling of hazardous materials must be observed, as defined in global regulations such as GHS (Globally harmonised system) directives and guidelines of the European Union and the rules and laws of the individual country. Safe storage cabinets In this context the most important regulation is BS EN 14470-1:2004: Fire safety storage cabinets. Safety storage cabinets for flammable liquids. Safety storage cabinets with a proven fire resistance class in accordance to BS EN 14470-1 help provide industries with a less risky local storage of toxic, flammable or potentially explosive substances in modern workplaces. A safety storage cabinet manufactured to BS EN 14470-1 provides a series of safety measures that protect the stored hazardous materials against the fire. First of all in the event of fire, the drawers as well as the doors close automatically through thermal release. If no door open arrest system is used, the doors must close automatically from every position when released. The doors close at 122° F maximum and the closing sequence is completed within 20 seconds – starting from any position. The automatic closing works using a fusible link. These fusible links are located within the door open arrest system. The ventilation spigots and the drawers. As a consequence, in the event of fire all mechanisms close automatically. Once the automatic drawer and door have closed, the air ducts will automatically shut. Following this, the gaps of the safety storage cabinet become totally sealed between the door and frame through special intumescent seal protection strips which, when exposed to fire, expand and seal hermetically to avoid heat entering the cabinet. Jointly, the steel body and the insulation within prevent a critical temperature increase inside the cabinet – the steel body alone does not offer any protection and in fact it is a strong heat conductor. Underneath the robust steel surface are multiple layers of fireproof mineral fibre insulation material and these insulation boards prevent temperature increase within the cabinet. Some safety storage cabinets can with stand fire over a time period up to 90 minutes. In spite of the fact that this heavy exposure to temperatures exceeds 1,000°C, the containers used for storing flammable liquids and hazardous materials remain safe and perfectly intact. Only such cabinets will allow sufficient time for the personnel to evacuate the premises and the firefighters to enter the building, preventing a minor and extinguishable fire from turning into an uncontrollable one. Alan Murray is chief executive of the British Safety Industry Federation. For more information, visit www.bsif.co.uk |
|
|
|
Safety first | 15/03/2018 |
Many employers are unaware of their responsibilities when it comes to issuing Respiratory Protective Equipment (RPE) to their workforce, and in particular what their responsibilities are surrounding Fit Testing, warns Alan Murray. FIT TESTING is a method for checking that a tight fitting facepiece matches the wearer’s facial features and seals adequately. The performance of tight-fitting facepieces depends on filtering technologies and achieving a good seal between the wearer’s skin and the mask, therefore wearing an inadequately fitting mask that is the wrong size will significantly reduce the protection provided and could put the wearer’s health, or even life, in danger. The HSE has produced a detailed guide on Fit Testing called: OC282/28. Initially produced for their inspectors this document is publicly available on the HSE website and answers many of the most commonly asked questions. It states that Fit Testing can only be carried out by a “competent person” and it gives definite guidelines as to what knowledge this competent person should have. It is not possible to nominate “Mr Smith” because he knows more about masks than anyone else. A competent person must have a thorough understanding of RPE, from the initial selection process, to identifying poorly maintained or fitting RPE, through to a good knowledge of Fit Testing and the various methods available. Complying with the law One of the most common questions we get asked is, “Do I need to Fit Test my workforce?” The answer is yes. It’s a legal requirement that workers using tight fitting RPE as a control measure under health and safety legislation must be fit tested. This requirement is detailed in the CoSHH regulations and the associated ACOPs. An example of a mask that does not require Fit Testing would be a loose-fitting hood. If a mask is being used for comfort purposes and not as a control measure then a Fit Test is not required but this should be clearly demonstrated in the employers risk assessment. Is a Pre-use Fit Check the same as a Fit Test? No, a pre-use Fit Check is a method of checking that a face mask has been fitted correctly and should be carried out each time the mask is worn and prior to entering a hazardous environment. An example of a Fit Check on a half mask would be to cover-up or close off the particulate filters and take a deep breath in. If the mask is a good fit then you will see and feel the mask contract to the face. A Fit Check should also be conducted as part of the Fit Test process after the mask is applied and should form part of the educational process. In a recent statement released by the HSE they confirm that the only recognised methods of Fit Testing are the qualitative and quantitative Fit Test methods described in OC 282/28. By not Fit Testing or by using an un-validated method you could receive enforcement action from the HSE. Another common reason for failing a Fit Test is the presence of facial hair and stubble on the test subject. The HSE have published a report into the effect that facial hair and stubble has on the efficiency of RPE, it showed that even stubble which was present 24 hours after shaving can impact on the efficiency of RPE. Educating RPE wearers on the importance of being clean shaven should form part of the Fit Test process and many companies are now introducing clean shaven policies as a result. In a bid to increase the proficiency of Fit Testing within the UK the BSIF have developed an accreditation scheme to help validate competency; the Fit2Fit RPE Fit Test Providers Accreditation Scheme. The scheme is supported by the HSE, following this scheme is not compulsory and employers are free to take other action to comply with the law. But if you follow this scheme, you will be doing enough to demonstrate good practice. As you can see there is a lot more to Fit Testing than you’d initially expect. Knowledge, experience and technique are all extremely important in the application of a good Fit Test and it is essential not to forget that a poorly executed Fit Test could result in a person wearing a mask that is not suitable for them and does not offer them the level of protection assumed. Alan Murray is CEO of the British Safety Industry Federation. For more information, visit www.bsif.co.uk |
|
|
|
Controlling site spills | 04/11/2017 |
Based on experience from the USA and stringent UK regulations, Alan Murray makes recommendations for tackling spills control when extracting shale gas. RISING LIVING standards and increasing use of personal computers, smart phones and tablets all mean energy consumption in the UK continues to rise. Conservation of energy through smart meters, improved fuel efficiency, and home insulation has had great effect in modifying demand, and such measures will continue to limit energy consumption, but they will not stop it increasing. At the moment, UK energy supplies are provided by natural gas (40%), coal (10%), nuclear power (25%), biomass (12%) and renewables (12%). With climate change targets, the closure of coal mines, concerns surrounding nuclear power and the high cost of renewables, Britain needs additional diverse sources of energy. Enormous effort is going into new technology such as clean gas power stations, thermo-voltaic light, new battery developments and seismic surveying, which will alter the relative attractions of nuclear, gas, and renewable sources, but predicting which technology will meet the increased demand at a sensible cost with acceptable carbon emissions is difficult. No single source will supply all our requirements, and cost is important. Four million households in the UK live in fuel poverty, and the UK’s current energy costs are some of the highest in the world. One option under consideration is the extraction of shale gas. It is argued that the cost of British shale gas would be low because:
But a new industry would bring its own set of requirements on pollution control to avoid environmental spills. All energy sources, gas, coal, nuclear, biomass, and renewables carry environmental risks. Environmental concerns around shale gas focus on:
Setting up a drilling site would need heavy equipment, sand and other inputs, causing initial disruption, and the drilling typically takes several weeks, but then gas production would go on for decades with few lorry movements. However, a major concern is the heavy goods vehicle transportation of the large volumes of flowback water created, and the BSIF Liquid Pollution Control Group agrees with leading shale gas companies that the water should be processed on site. Contamination of groundwater is a risk, but a peer reviewed study of contamination of groundwater by Duke University (The Effects of Shale Gas Exploration and Hydraulic Fracturing on the Quality of Water Resources in the United States by Avner Vengosh et al) found fracking has not contaminated ground water. However, the study did find that accidental spills of fracking waste water could be dangerous to surface water in the area. This could become a risk to groundwater through seepage into the ground if there is no liner across the site. Both surface water and groundwater should be adequately protected, but groundwater is especially challenging and more costly to remediate once pollution has occurred. Some extraction activities are quoted as giving rise to environmental issues, when in fact they have already been addressed in the UK in regulations. The following activities are not allowed in the UK: Injection of hydraulic fracturing fluids directly into groundwater resources, discharge of inadequately treated fracturing wastewater to surface water and disposal or storage of hydraulic fracturing wastewater in unlined pits. If extraction of shale gas is permitted in Britain, the BSIF Liquid Pollution Control Group recommends that flowback water from fracking should be treated on or near site to minimize vehicle movements and the associated disruption. Spill control measures will be site-specific but they should reflect the requirements of the Environment Agency’s Onshore Oil & Gas Sector Guidance Version One. They should also be relevant to recommendations from CIRIA 736 Containment systems for the prevention of pollution. The should encompass the best available technologies developed for shale gas sites, especially from the USA experience. Spill awareness and response training should also be provided by accredited organisations to all site operators. The BSIF is working with UK Onshore Oil and Gas to promote accredited training and spread of best practice. Alan Murray is chief executive officer of the British Safety Industry Federation. For more information, visit www.bsif.co.uk |
|
|
|
BSIF Networking Day a "great success" | 09/10/2017 |
THE BSIF Networking Day was deemed "a great success" by delegates who attended this year's annual event at Oulton Hall in Leeds. Taking place on Thursday 28th September, attendees enjoyed a full day of activities at the spectacular venue, with a gala dinner in the evening. John Gill, chairman of the BSIF welcomed attendees at a BSIF briefing, hosted by BSIF CEO, Alan Murray and the Federation's general manager, Frank Angear. "We are delighted with the expansion in BSIF membership," John announced. "This highlights the importance of focusing on quality and PPE compliance and I'd like to take this opportunity to tell the industry to be outspoken and drive the story of PPE quality." Alan Murray added that the Federation's key challenge was to rebuild the image of the safety and health industry. "In our Federation Strategy which we launched last year we focused on key pillars to give our members and the market the best trade body possible – one that they deserve and would be proud be part of," Alan explained. "The pillars and the activities within them properly executed will deliver the best Federation in the country. "These were expressed as rebuilding the image of our industry, driving and leading on standards development; creating and sharing expertise on OS&H issues; enhancing the quality of PPE & safety products, giving reassurance to the market; educating our members so that they can demonstrate their expertise and value as suppliers; and develop and grow the membership to be 75% of the UK industry, a critical mass, so that we always get the ear of the legislators." Alan noted that the image of safety and health is too often negative, citing the public reaction when Big Ben was shut down: "Never mind working in 120 decibels bonging off every 15 minutes," he observed. "In the UK over 30million working days are lost to injury illness and ill health. We determined that the only way forward was to consistently promote what we all know to be true and that is that good safety and health is good for business, whether the business is big or small. We have been really successful in getting time with MPs and getting their ear and we currently have meetings planned with about 15 MPs." The BSIF has successfully inspired two Early Day Motions on the message and gained support for its Registered Safety Supplier Scheme. "At parliamentary receptions we have launched the Respiratory Report which highlights that occupational health is in fact part and parcel of public health overall," added Alan. "We have increased our use of digital media and our partnership with Western Business Publishing & Exhibitions (WBPE) means that our messaging reaches more than 30,000 new readers. We are determined to celebrate this vital industry in which we work and all the good that you do out there." With the new PPE Regulation becoming applicable in less than seven months, the BSIF has been working with the European and UK authorities in supporting its implementation. Updating its “Countdown” pamphlet and working with ESF, the Federation has produced a flowchart to illustrate what it means to all the commercial operators in the market. "We have broken this out into a 'Step by Step' presentation which we will present at Health and Safety North, Event City in Manchester on 10 and 11 October," Alan continued. I would recommend that you are there as it should be really helpful and will be a great event. "A lot of our communications with Westminster, including meetings with the Department for Exiting (DexEU), have included Brexit issues and the future of the standards regulations and structures which our industry has operated under for the last 25 years. This continues and, regardless of the reassurances under Withdrawal Bill, we remain watchful on the inevitable divergence of laws over time. "The BSIF Product and Working Groups are a unique opportunity for the members to stay abreast and influence standards in this country and beyond and our Product Groups are being redefined as Special Interest Groups with routes planned and agreed for participation on PH, ISO and CEN committees. We have created a new web based platform to facilitate the whole process." With BSI certification, the BSIF has for the first time co published guidance to an EN Standard - in this case the revised EN 388 - and has also increased the scope of working groups / special interest groups, including a group focusing on measurement and instrumentation. "We are also encouraging more participation from sales and marketing as well as technical functions," noted Alan."The third pillar of our strategy is the development and sharing of expertise on a range of crucial occupational safety and health issues. According to Alan, to some extent this started out as a counter balance to the very heavy focus that 'health' was given within the HSE’s 2016 strategy and concerns that the message implied that 'safety was sorted'. However, the BSIF has embraced and supported the HSE strategy with its priorities: occupational lung disease, muscular skeletal disorder and work related stress. Nevertheless, the Federation continues to reinforce the value of the relationship between safety and health. "Respiratory protection is a very good example," Alan observed. "Wearing RPE would be seen as a safety measure whereas developing a respiratory disease would be seen as a health outcome. We have kept a strong focus on developing the F2F community which now has over 300 accredited providers - 20% up on this time last year. About nine months ago we held a one day seminar for Fit 2 Fit providers and more than 100 people attended. The Fit2Fit organisation is also heavily involved in the new HSE Industry Guidance and will be publishing in April 2018. In support of the membership and sharing expertise, BSIF will be publishing industry papers each year on critical safety and health issues. The first publication that is planned is the BSIF document on Muscular Skeletal Disorders. We have also maintained and strengthened our relationships with other key stakeholders in this area, such as BOHS, IIRSM, IOSH, ROSPA and the Safety Groups UK organisation. "Our next area of focus within the strategy was the area of education. This is education on the basis of inform, accredit and qualify the membership so that they can clearly demonstrate expertise and differentiate their offer to clients. The Safe Supply Qualification is now developed and being piloted. This course and qualification delivered primarily online will be a publicly accredited qualification for customer facing staff of BSIF members illustrating capability to your clients. This is the foundation of safe supply and we have plans in the future to add additional modules for expertise in specific areas. Again, working with the HSE, there is a proposal to develop a Respiratory module to help educate the market and the user. "We also provide a BSIF approval scheme for training content from Face Fit companies and, similarly, there is also an approval scheme for Spill Control training programmes. Perhaps one of the most exciting developments in this area has been the creation of an NVQ in Permanent Fall Arrest Systems as different construction trade cards have been withdrawn. This has been submitted to the Dept for Apprenticeships as part of the lifelong apprenticeship initiative and should allow companies to receive 90% funding for this training. All of this is designed to improve the capability of the membership and to be able to demonstrate that capability to clients. Alongside capability comes quality of product." Frank Angear observed that adoption of the BSIF Registered Safety Supplier (RSS) Scheme has increased rapidly this year. The RSS Scheme is the vehicle to provide the market with reassurance on the quality of PPE and safety products. "One year ago there were 40 members who were registered in the scheme," Frank explained, "now there are nearly 120. As well as publishing commitments in quality manuals, qualifying staff in safe supply and submitting to CE documentation audits, Registered Safety Suppliers also now submit to random product testing against EN clauses where claims are made. We are well into this programme and it is proving of value with some key products failing to perform. The suppliers have all reacted appropriately and the users have been protected." "I am delighted to tell you that the Federation has a Primary Authority coordinated partnership with Hertfordshire TS," Alan announced. "What this means is that as a member of BSIF you share in the agreement and the benefits. The official start date of this agreement is 1 October and we will write out on what this entails. You will all as members be able to use the Primary Authority logo which we of course encourage you to do. The Registered Safety Supplier Scheme is vital in enhancing quality and capability in the market but really needs specified by users to create awareness and demand and we need to work together on this." The BSIF has developed a website www.registeredsafetysupplier.co.uk for end users to demonstrate their support for the scheme and to receive BSIF resources. The site incorporates a "Find a supplier" search function (by postcode) where all the RSSS members are listed. "We want as many users as possible to support the scheme," said Alan. "This will make it demanded in the market. We promote the scheme under the banner of 'Anyone can sell safety but you wouldn’t buy safety from Anyone'. We need your help on RSSS at end user level to get support and create this shout. We really do need to work together on having the Registered Safety Supplier Scheme being demanded by users - it is a prize, so worth having." Alan concluded: "This is about the result of the work that is being done. Being clear on our message and clear on the communication allows us be make sure the relevance of the Federation is obvious. Growth is not an end in itself, it is a result of the work that is being done in the market. That result is very positive with more than 200 companies now members of the Federation." Tim Else, events director at Western Business Exhibitions, explained to the audience how the new strategic partnership with the BSIF was increasing exposure via a multitude of media outlets. "Together we have enjoyed a long relationship lasting 18 years. Last December we signed this new agreement which will increase the Federation's exposure through print, online, webinars and exhibitions. The BSIF's presence at our Health & Safety Events has been greatly enhanced and we are also combining our forces to host the Safety & Health Excellence Awards on 11 April 2018 at Vox, Resorts World, Birmingham." Following a networking lunch, afternoon proceedings got underway with a golf tournament and networking activities, including segueway races and 'Krypton Factor'-style challenges. The evening commenced with a gala dinner, at which two awards were handed out - Hugo Watts winning the BSIF Commitment to Federation Activities Award and Peter Nicholls taking the prize for BSIF Outstanding Contribution Award 2017. Those who attended the event described it as a "great success" and "a fantastic way to network with industry colleagues in a relaxed setting." For more information on the BSIF and the RSS Scheme visit www.bsif.co.uk/ |
|
|